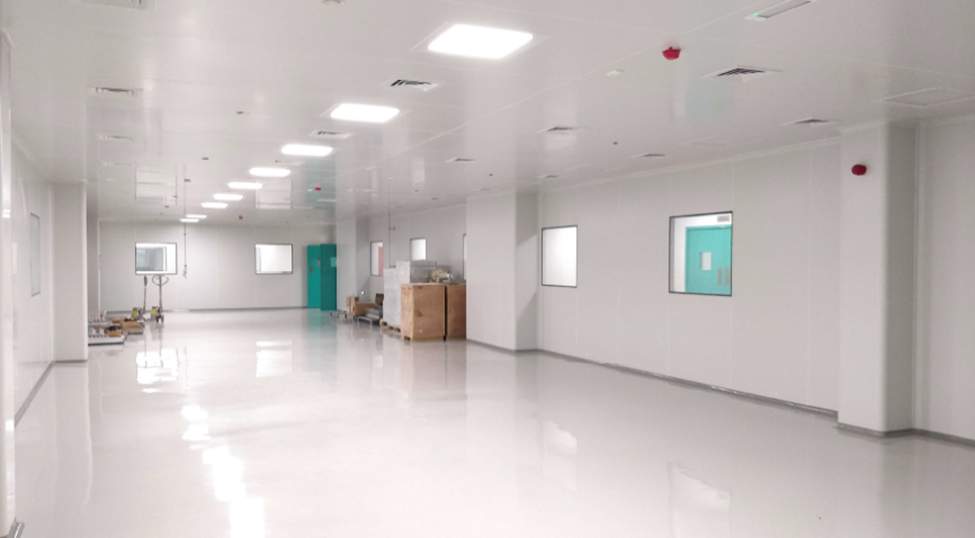
In the realm of medical laboratories, maintaining an environment free from contaminants is paramount. Cleanrooms are specialized controlled spaces designed to uphold stringent cleanliness standards, ensuring the integrity of medical research, device manufacturing, and pharmaceutical production.
Understanding Cleanroom Classifications
Cleanrooms are categorized based on the International Standards Organization (ISO) 14644-1 standards, which define cleanliness levels by specifying the allowable concentration of particles per cubic meter of air. The classifications range from ISO Class 1 (the cleanest) to ISO Class 9 (comparable to typical room air). Medical laboratories typically operate within ISO Classes 5 to 8, depending on their specific requirements.
- ISO Class 5: Permits up to 3,520 particles (≥0.5 microns) per cubic meter.
- ISO Class 6: Allows up to 35,200 particles.
- ISO Class 7: Permits up to 352,000 particles.
- ISO Class 8: Allows up to 3,520,000 particles.
These classifications dictate the design and operational protocols of cleanrooms to ensure compliance and maintain the desired level of cleanliness.
Key Features of Medical Laboratory Cleanrooms
To achieve and maintain the required cleanliness standards, medical laboratory cleanrooms incorporate several critical features:
- Advanced Filtration Systems: Utilization of High-Efficiency Particulate Air (HEPA) filters effectively traps airborne particles, including dust, bacteria, and microorganisms, ensuring a contaminant-free environment.
- Controlled Airflow: Implementation of unidirectional airflow prevents the recirculation of contaminants by directing air in a single pass, reducing the risk of cross-contamination.
- Stringent Environmental Monitoring: Regular monitoring of parameters such as temperature, humidity, airborne particle counts, and pressure differentials ensures that cleanroom conditions remain within specified limits.
- Specialized Cleanroom Garments: Personnel wear garments designed to minimize particle shedding, including gowns, masks, gloves, and shoe covers, to maintain hygiene and prevent contamination.
- Regular Surface Decontamination: Routine cleaning of surfaces with appropriate agents prevents microbial build-up, maintaining the sterility of the environment.
- Controlled Entry and Exit Protocols: Use of airlocks and gowning rooms limits exposure to external pollutants, with strict procedures for personnel movement to maintain cleanliness.
- Material Compatibility: The selection of non-porous, easy-to-clean materials for surfaces and equipment minimizes particle retention and microbial growth.
- Comprehensive Personnel Training: Staff undergo extensive training in cleanroom protocols, hygiene practices, and standard operating procedures to prevent contamination.
Types of Medical Laboratory Cleanrooms
Medical laboratories utilize different types of cleanrooms based on their specific applications:
Medical Research Cleanrooms
These facilities support research and experimentation, often requiring ISO Class 5 to 7 environments. They are designed to be safe, with safeguards against biosecurity risks, and may include negative pressure systems to prevent the escape of harmful substances.
Medical Device Manufacturing Cleanrooms
The production, assembly, and packaging of medical devices necessitate controlled environments to prevent contamination. Depending on the criticality of the devices, these cleanrooms operate within ISO Class 5 to 8 standards, with stricter controls for devices that come into direct contact with patients.
Pharmaceutical Cleanrooms
Involved in the development and testing of pharmaceutical products, these cleanrooms require stringent controls to prevent contamination that could affect product efficacy. They typically adhere to ISO Class 5 or higher standards and comply with additional regulations such as the U.S. Pharmacopeia (USP) standards, including USP 797 for sterile non-hazardous compounding and USP 800 for sterile hazardous compounding.
Design Considerations for Medical Laboratory Cleanrooms
Designing a cleanroom for medical laboratory applications involves careful planning to meet specific cleanliness requirements:
HardWall Construction
HardWall cleanrooms offer robust control over environmental factors and can be customized to include features necessary for various medical applications. They are suitable for complying with the strictest medical cleanroom classifications.
HVAC Systems
A powerful Heating, Ventilation, and Air Conditioning (HVAC) system is essential to regulate temperature, humidity, and air pressure, ensuring a stable environment.
Laminar Airflow Patterns
Designing airflow patterns that facilitate laminar flow helps in efficient removal of contaminants and maintains air purity.
Cleanroom Lighting and Furniture
SThe selectionof appropriate lighting and ergonomic furniture that integrates seamlessly with the cleanroom layout supports operational efficiency while maintaining cleanliness standards.
Read Also: Top Cardiologist and Female Dermatologist in West Palm Beach
Conclusion
Cleanrooms are indispensable in medical laboratories, providing controlled environments that ensure the sterility and precision required for medical research, device manufacturing, and pharmaceutical production. By adhering to stringent classification standards and incorporating advanced design features, cleanrooms uphold the integrity of critical medical processes, ultimately contributing to improved healthcare outcomes.