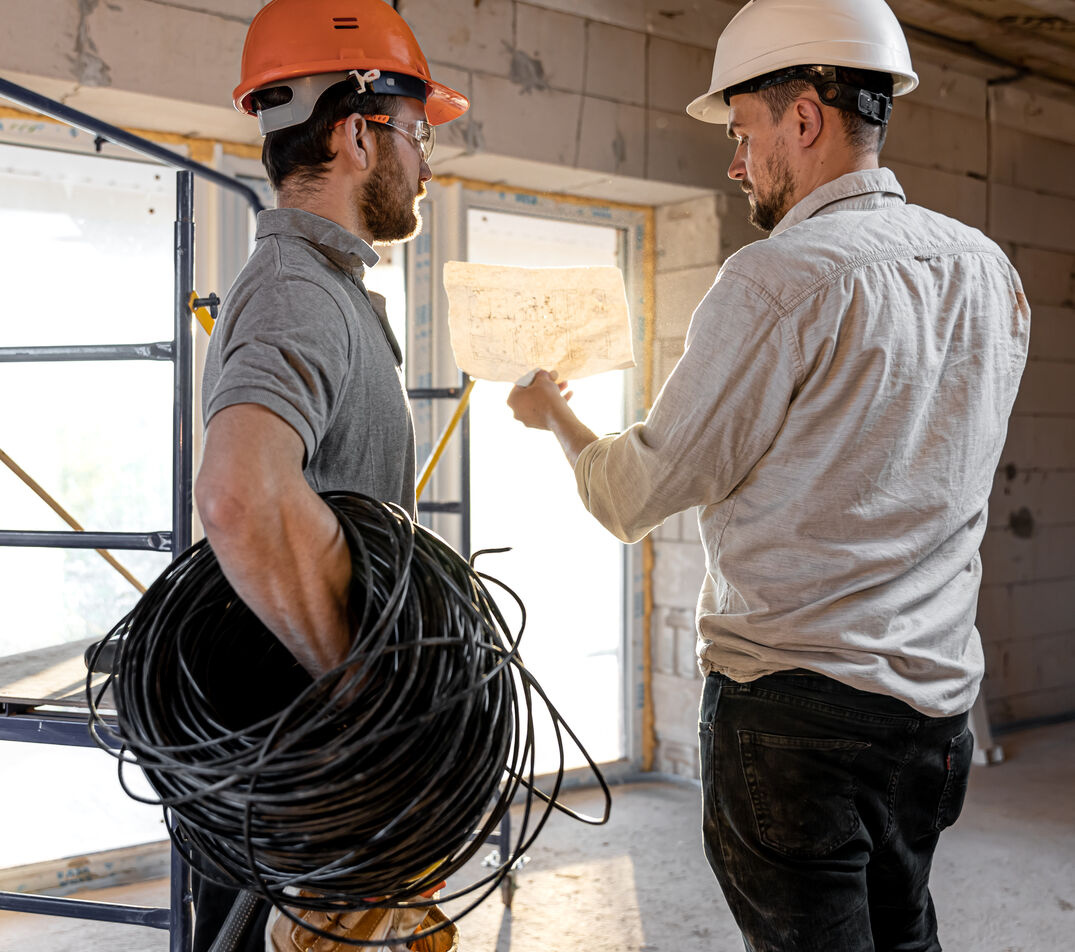
Assembly line systems have become one of the most influential concepts in the modern manufacturing world. These systems have redefined the way products are made, drastically improving speed, consistency, and overall efficiency. From automotive factories to electronics assembly, assembly line systems have proven essential for businesses aiming to meet large-scale production demands while maintaining high standards of quality.
What is an Assembly Line System?
An assembly line system is a manufacturing process in which individual components of a product are progressively added in a sequential manner, typically using mechanized tools or automated machinery. The system works on the principle of division of labor, where each worker or machine performs a specific task, leading to the creation of a finished product. The assembly line is often associated with the concept of mass production, where large quantities of identical items are produced at high speeds.
History of Assembly Line Systems
The concept of the assembly line can be traced back to the early 20th century, with one of the most notable pioneers being Henry Ford. In 1913, Ford revolutionized the automobile industry by introducing the moving assembly line at his Highland Park plant in Michigan. This method dramatically reduced the time it took to assemble a car from over 12 hours to just about 90 minutes. Ford’s innovation didn’t just change the automobile industry; it also set the stage for mass production in various sectors.
Before Ford’s introduction of the moving assembly line, most products were made by skilled craftsmen or in small batches. The assembly line approach allowed for the automation of much of the manufacturing process, which in turn resulted in greater productivity, lower costs, and the ability to meet growing demand.
Types of Assembly Line Systems
Assembly line systems come in various configurations, each suited to different production needs. Understanding the different types of systems is crucial for companies to select the best method for their manufacturing processes.
1. Manual Assembly Lines
In a manual assembly line system, workers are responsible for performing individual tasks along the production line. Each worker typically completes a specific, repetitive job that is part of the overall assembly process. While this system can be slower and less efficient than fully automated systems, it is ideal for products that require a high level of craftsmanship or customization.
Manual assembly lines are often used in industries such as electronics, furniture, and small-scale manufacturing where manual labor is needed for intricate tasks.
2. Automated Assembly Lines
Automated assembly lines are characterized by the use of robotics and other automated machinery to perform tasks such as welding, part placement, and packaging. This system is highly efficient and can work at a faster rate compared to manual lines. The main benefit of automated assembly is its ability to perform tasks with precision, consistency, and minimal human intervention.
Automated systems are most commonly used in large-scale production environments, including the automotive industry, where robots are used to perform tasks such as engine assembly, welding, and painting.
3. Flexible Assembly Lines
Flexible assembly lines, or “lean” assembly lines, allow for the production of a variety of products without requiring a complete overhaul of the production process. These systems are highly adaptable and can be reconfigured to accommodate changes in product design or production volumes.
In a flexible assembly line, machines and tools are easily adjustable to accommodate different tasks, making this system an excellent choice for industries that require frequent changes in product models, such as the electronics and appliance sectors.
4. Continuous Flow Assembly Lines
Continuous flow assembly lines are used for manufacturing products that are produced in a continuous sequence, such as beverages, chemicals, and pharmaceuticals. The main advantage of this system is its ability to produce large quantities of a single product at a consistent rate.
This type of assembly line is often found in industries where products are manufactured in bulk and require minimal variation during the production process. It is typically highly automated and designed to operate 24/7, maximizing output.
Components of Assembly Line Systems
Assembly line systems typically consist of several key components that work together to create a smooth and efficient production process. These components can vary depending on the type of assembly line, but some common elements include:
1. Conveyor Belts
Conveyor belts are essential components of most assembly line systems. They serve as the mechanism that moves products along the production line from one workstation to the next. Conveyor belts can be manual or powered, depending on the complexity of the assembly process. Automated conveyor systems help reduce downtime and ensure a steady flow of materials through the production process.
2. Workstations
Workstations are the individual work areas where specific tasks are carried out. Depending on the system, a workstation might involve manual labor, robotic automation, or a combination of both. The tasks performed at each workstation depend on the type of product being produced and the overall assembly line design.
3. Robots and Automated Machinery
Robots and automated machinery are used in more advanced assembly line systems to carry out tasks such as welding, painting, and part assembly. Robots can be programmed to perform repetitive tasks with great precision and speed, improving the efficiency of the assembly process.
4. Assembly Line Control Systems
Modern assembly lines rely on sophisticated control systems to monitor and manage the entire production process. These control systems ensure that the various components of the assembly line work in harmony and that products meet the desired specifications. In some cases, real-time data analytics is used to track performance, identify bottlenecks, and optimize the production flow.
Benefits of Assembly Line Systems
There are numerous advantages to adopting an assembly line system, making it an attractive option for manufacturers across various industries.
1. Increased Production Speed
One of the most significant benefits of an assembly line system is the increase in production speed. By dividing the manufacturing process into smaller, repetitive tasks, products can be assembled at a faster pace. In some cases, the assembly time can be reduced by 50% or more, allowing businesses to meet high demand levels.
2. Lower Labor Costs
Assembly line systems are often highly automated, meaning that fewer workers are needed to complete the production process. This can result in significant cost savings, as businesses can produce more with fewer labor hours. Additionally, automated systems can work 24/7 without the need for breaks or shift changes, further increasing efficiency.
3. Improved Product Quality
The consistency and precision offered by assembly line systems often lead to improved product quality. With fewer variables in the production process, defects and errors can be minimized. Automation, in particular, allows for tasks to be performed with high accuracy, ensuring that each product meets the required standards.
4. Flexibility and Scalability
Assembly line systems are often flexible, allowing manufacturers to produce a wide range of products or adjust production volumes as needed. Whether a company needs to produce a small batch or ramp up production to meet growing demand, assembly lines can be reconfigured or expanded to suit the needs of the business.
Challenges of Assembly Line Systems
While assembly line systems offer numerous benefits, there are also some challenges that manufacturers must address when implementing these systems.
1. Initial Setup Costs
Setting up an assembly line system can be costly, particularly if automation and robotics are involved. Companies need to invest in specialized machinery, tools, and control systems, which can require a substantial upfront investment. However, the long-term savings in labor and increased efficiency often offset these initial costs.
2. Maintenance and Downtime
Like any complex system, assembly line systems require regular maintenance to keep them running smoothly. A malfunction in one part of the system can cause significant delays in production, which can be costly. Regular maintenance schedules and contingency plans are essential to minimize downtime and ensure that the production line remains operational.
3. Worker Training
Although automation plays a significant role in modern assembly lines, human workers are still essential to the process. Workers must be trained to operate machinery, troubleshoot issues, and ensure quality control. Ensuring that workers have the necessary skills and knowledge is crucial for the success of the system.
Future Trends in Assembly Line Systems
As technology continues to advance, the future of assembly line systems looks promising. One of the most notable trends is the increased use of artificial intelligence (AI) and machine learning to optimize production processes. AI can be used to predict maintenance needs, identify inefficiencies, and adapt the system in real-time for maximum productivity.
Additionally, the rise of Industry 4.0, which focuses on smart manufacturing and the Internet of Things (IoT), is poised to further revolutionize assembly line systems. IoT-enabled devices can communicate with each other and provide real-time data, allowing for more streamlined and efficient production processes.
Conclusion
Assembly line systems have been instrumental in shaping the manufacturing landscape, providing businesses with the tools needed to produce high volumes of products quickly and efficiently. With their numerous benefits, including increased production speed, lower labor costs, and improved product quality, assembly lines continue to be a cornerstone of modern manufacturing. As technology advances, assembly line systems will become even more sophisticated, further improving efficiency and driving innovation across various industries.