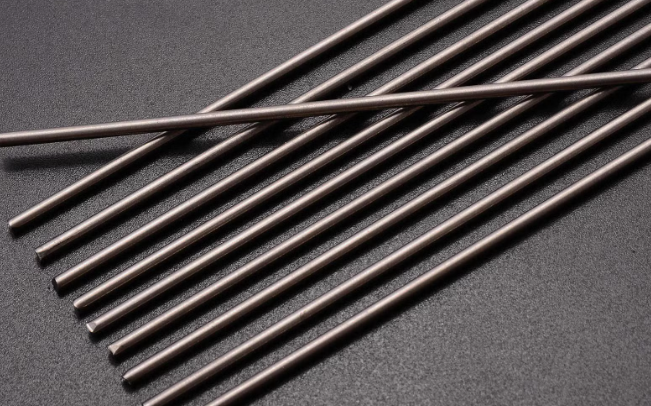
Titanium welding is widely used in industries like aerospace, automotive, and medical equipment due to its high strength, corrosion resistance, and lightweight properties. However, welding titanium presents several challenges that require specific techniques and precautions. In this guide, we will discuss the most common issues encountered when using Titanium Welding rods and provide solutions to ensure successful welding.
Common Challenges in Titanium Welding
1. Contamination Issues
Challenge: Titanium is highly reactive at high temperatures and can easily absorb contaminants like oxygen, nitrogen, and hydrogen. This contamination leads to brittle welds, cracks, and discolouration.
Solution:
- Use high-purity shielding gas, such as argon or helium, to create an inert atmosphere.
- Ensure all welding tools, gloves, and surfaces are free from oil, moisture, and dirt.
- Use a trailing shield or gas cup extension to protect the weld until it cools.
2. Maintaining an Inert Atmosphere
Challenge: If titanium welds are not adequately shielded, they can oxidize and become weak.
Solution:
- Use a dedicated welding chamber or a high-quality purge system.
- Ensure continuous gas coverage before, during, and after welding.
- Avoid drafts or airflow disturbances that may introduce oxygen into the weld area.
3. Choosing the Right Titanium Welding Rod
Challenge: Selecting the wrong filler metal can lead to weak joints or mismatched mechanical properties.
Solution:
- Match the filler rod to the base metal. For example, Titanium Welding Rods with grades like ERTi-2 and ERTi-5 are commonly used.
- Consult with a Titanium Welding Rod Supplier to source the correct material for your application.
4. Heat Control and Distortion
Challenge: Titanium has a low thermal conductivity, making it prone to overheating and warping.
Solution:
- Use a lower heat input with controlled welding parameters.
- Implement pulsed TIG welding to reduce heat buildup.
- Preheat and post-weld treatments are generally not required but maintaining an even heat distribution helps prevent warping.
5. Cracking and Porosity
Challenge: Improper welding techniques can lead to porosity and cracking in titanium welds.
Solution:
- Use a steady welding technique with minimal stop-start motions.
- Ensure proper gas shielding to prevent air contamination.
- Store welding rods in a dry, sealed environment to prevent moisture absorption.
Best Practices for Titanium Welding
- Use clean equipment: Any dirt or contamination can weaken the weld.
- Maintain proper shielding gas coverage: Poor shielding results in oxidation and weak welds.
- Choose the right welding rod: Consult a reliable titanium welding rod supplier to ensure you get high-quality filler material.
- Avoid excessive heat input: Titanium is sensitive to overheating, so use proper techniques to control temperature.
Conclusion
Titanium welding is a precise process that requires attention to detail. By understanding the common challenges and implementing the right solutions, you can achieve strong and defect-free welds. Whether you are a professional welder or working in an industrial setting, using high-quality Titanium Welding Rods from a trusted Titanium Welding Rod Supplier ensures optimal results. With proper techniques and materials, titanium welding can be performed successfully, leading to durable and high-performance welds.