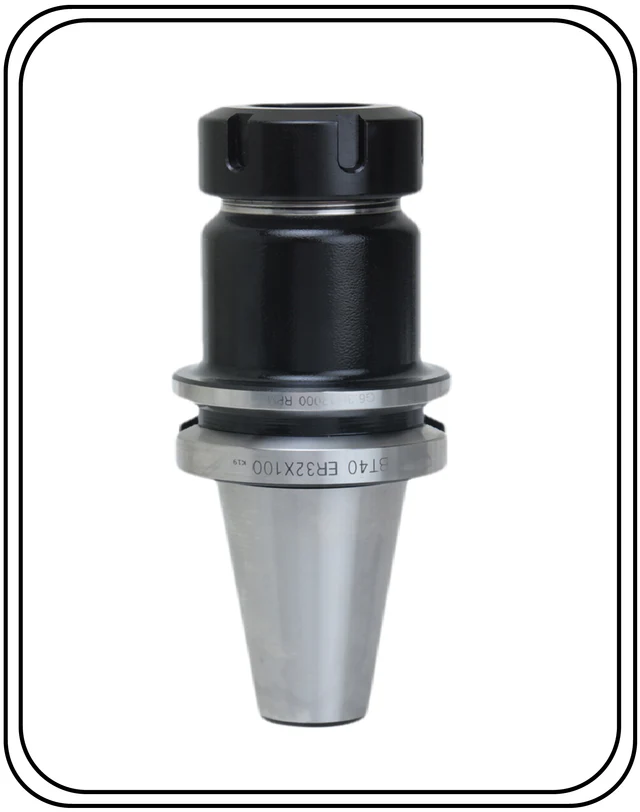
Introduction
In the realm of precision CNC and machining, the choice of the tool-holding systems can affect the result. One of the most popular tool holders on the market is the collet chucks. The collet chuck is known for its high precision and reliability, as well as its flexibility. A collet chuck is crucial to achieve optimal results when turning, milling, and drilling.
This guest blog post covers everything you must be aware of about collet chucks and how they function, what types are available, their advantages, and expert advice on picking the best one for your particular needs.
What is a collet chucks?
A collet chucks is a kind of chuck that uses collets — a flexible, slotted sleeve that is designed to hold securely an item or tool. As the collet gets tightened, it expands to grip the object with great concentration and accuracy. Collet chucks are commonly employed in CNC milling machines, lathes, grinders, routers, and lathes.
How Does a Collet Chuck Work?
The process is easy but efficient:
- A collet is inserted in the body of the chuck.
- A tightening nut exerts tension on the collet.
- The collet expands uniformly around the workpiece or tool and creates a firm and concentric grip.
This mechanism is more precise than different types of chucks, which makes it the ideal choice for high-speed and high-precision manufacturing.
Common Types of Collet Chucks
There are many types of collet chucks that are based on the type of machine and the application:
1. ER Collet Chuck
- Most often employed in CNC milling and drilling.
- Available in sizes ER8 to ER50.
- The name is synonymous with versatility and a wide gripping range.
2. 5C Collet Chuck
- Popular in turning and lathe operations.
- Offers excellent concentricity.
- The gripping limit is limited to a fixed range.
3. R8 Collet Chuck
- Most often, vertical mills are used, such as Bridgeport machines.
- The design is integrated and does not require a separate body for the chuck.
4. Autolock Collet Chuck (DA & OZ)
- Ideal for applications with high torque.
- Locks securely without slippage of the tool.
5. Hydraulic and Pneumatic Collet Chucks
- Automated for quick tool adjustments.
- Designed for high-volume manufacturing.
Advantages of Using a Collet Chuck
- High Accuracy High Accuracy: Superior control of runout guarantees a better finish on the surface and longer tool life.
- Compact Design: allows for use in tight spaces and small machines.
- Quick Tool Changes Reduces setup time and improves productivity.
- A wide variety of sizes can accommodate various shank diameters using the same chuck.
- Reduced Vibration: A uniform grip reduces chatter when machining.
Applications of Collet Chucks
Collet chucks are utilized in different fields and for various purposes:
Application | Machine Type | Common Chuck Type |
CNC Milling | CNC Machining Centers | ER Collet Chuck |
Turning | CNC Lathes | 5C Collet Chuck |
Precision Grinding | Grinding Machines | Hydraulic Collet Chuck |
Woodworking | Routers | ER or Spring Collets |
Metal Drilling | Drill Presses | DA Collet Chuck |
Choosing the Right Collet Chuck
Here are the most important aspects to take into consideration:
1. Machine Compatibility
Check that the collet chuck matches the spindle taper on your machine (e.g., BT, HSK, CAT, ISO).
2. Application Type
Utilize ER Chucks for general use 5C for lathes and hydraulic chucks for precision needs.
3. Grip Range
Pick a chuck that covers the diameter of your workpiece or tool to reduce the amount of inventory.
4. Runout Tolerance
If you’re machining with tight tolerances, you should choose an chuck that has <0.005mm runout.
5. Tool Change Frequency
If you require regular tool replacements, consider automatic or quick-change chuck systems.
Maintenance Tips for Collet Chucks
To get the most performance and longest life out of your collet chucks:
- Clean regularly Chips or dirt can impact gripping force and accuracy.
- Inspect for wear Check the surfaces of the collet and chuck for damage or cracks.
- Use the correct torque The overtightening of the bolt can cause damage to the spindle or collet.
- Lubricate Threads Reduce friction and prolong the lifetime of the threads and nut.
Common Mistakes to Avoid
- Use the wrong collet Size It can cause damaged or abrasive grip.
- The absence of maintenance leads to decreased accuracy and a risk to safety.
- Mixing Brands Always use collets and nuts of the same brand.
- The overloading of the chuck could cause damage to the collet as well as spindle.
Top Brands for Collet Chucks
When purchasing collet chucks, look for brands that are reputable and with a reputation for reliability and precision:
- Techniques
- Kennametal
- Sandvik Coromant
- Vertex
- EROWA
- HAIMER
Where to Buy Collet Chucks
You can buy high-quality collet chucks at:
- Industrial tooling suppliers
- CNC and dealers in machine tools
- E-commerce platforms such as MSC Direct, Amazon, AliExpress and IndiaMART
Always confirm the credibility of the supplier and request authenticity certificates if you require them.
Final Thoughts
A collet chuck is more than an instrument holder It’s a crucial component that directly affects the quality and effectiveness of your machine processes. It doesn’t matter if you’re a precise engineer, a workshop owner, or a CNC enthusiast; investing in the best collet chuck can result in better finishes, a longer lifespan for the tool, and less downtime.
With the many types available and the increasing importance of productivity, now’s the time to update or tweak your tool-holding strategies using the correct collet chuck.