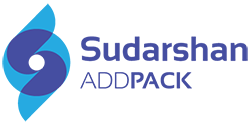
Introduction to Bulk Bags
Bulk bags, also known as FIBCs (Flexible Intermediate Bulk Containers), play a crucial role in transporting and storing heavy-duty materials across industries like agriculture, construction, and chemicals. Behind these versatile packaging solutions are expert bulk bag manufacturers who ensure durability, safety, and sustainability at every stage. One of the leading names in the field Sudarshan Addpack, stands out for its innovation, high-quality standards, and eco-friendly practices. In this article, we’ll explore the complete lifecycle of a bulk bag — from manufacturing to reuse and recycling — and highlight how top manufacturers are shaping the future of industrial packaging.
Role of Bulk Bag Manufacturers
Who Are Bulk Bag Manufacturers?
Bulk bag manufacturers are the masterminds behind the scenes. They engineer, design, test, and produce these industrial workhorses. It’s not just about stitching up fabric — it’s about precision, safety, and endurance.
Spotlight on Sudarshan Addpack
One name that stands tall in this industry? Sudarshan Addpack. They’re a trusted bulk bag manufacturer known for their innovative designs, robust production standards, and eco-friendly approach. If you’re dealing with bulk transport, they’re the people you want on your side.
Stage 1 – Designing the Bulk Bag
Understanding Client Requirements
Every industry has unique needs. Some need bags for food-safe environments; others need bags that resist chemicals. The design phase ensures each bag is tailor-made, from dimensions to lifting loops.
Types and Styles of Bulk Bags
There’s no one-size-fits-all here. Bulk bags come in various configurations based on load type and handling requirements.
U-Panel, Circular, Four-Panel, Baffle Bags
-
U-Panel Bags – Basic and economical.
-
Circular Bags – No side seams = extra strength.
-
Four-Panel Bags – Squared shape for stability.
-
Baffle Bags – Internal baffles hold the bag shape even when full, perfect for stacking.
Stage 2 – Material Selection
Polypropylene: The Backbone of FIBCs
Most bulk bags are made from woven polypropylene – a durable, flexible plastic that’s lightweight yet strong. It resists moisture, mildew, and most chemicals.
Coated vs. Uncoated Fabrics
-
Coated Bags – For fine powders, to prevent leaks.
-
Uncoated Bags – Breathable, ideal for products that need airflow.
Stage 3 – Manufacturing Process
Extrusion and Weaving
It starts with melting polypropylene into threads, which are woven into fabric. Think of it like weaving a giant, super-strong cloth.
Cutting and Sewing
The fabric is cut to size, then stitched into the required design — including lifting loops, filling spouts, and discharge valves.
Printing and Finishing Touches
Companies often print logos, handling instructions, and certifications directly onto the bag. Then, the bags get pressed and packed for shipping.
Stage 4 – Quality Assurance and Testing
Stress Testing and Safety Factors
Bulk bags carry serious weight, so every bag is tested for load-bearing capacity, stitching integrity, and structural balance. Manufacturers often follow a 5:1 or 6:1 safety factor.
International Standards Compliance
Bags must comply with global standards like ISO, UN, or BRC, especially if they’re handling food, chemicals, or hazardous materials.
Stage 5 – Distribution and Usage
Logistics and Delivery
Once cleared, the bags are packed and shipped — often in compressed bales to save space. Speedy and secure delivery ensures supply chains stay smooth.
Industries That Use Bulk Bags
-
Agriculture (grains, seeds)
-
Chemicals and mining
-
Construction (cement, sand)
-
Pharmaceuticals
-
Food and beverage (sugar, flour)
Stage 6 – Reuse and Maintenance
How Many Times Can a Bulk Bag Be Used?
Some are designed for single use, others for multi-trip use. Multi-trip bags are made with extra reinforcement and undergo periodic inspection.
Cleaning and Inspection
Reusable bags must be cleaned and checked for wear, UV degradation, or stitching damage. One weak loop and you’ve got a spill risk.
Stage 7 – Recycling Bulk Bags
End-of-Life Options
Once a bulk bag is beyond reuse, it doesn’t have to head to the landfill. Polypropylene is fully recyclable. It’s shredded, melted, and remolded into new products like furniture, mats, or even new bags.
Environmental Benefits of Recycling
Recycling saves energy, reduces emissions, and minimizes plastic waste. It’s a win for the company and the planet.
How Sudarshan Addpack Leads in Sustainability
Eco-Friendly Manufacturing Practices
Sudarshan Addpack integrates energy-efficient machinery, minimizes waste, and uses recyclable materials throughout production.
Innovations in Reusability and Recycling
They also invest in R&D to make bags more durable, easier to clean, and simpler to recycle — helping clients meet sustainability goals without sacrificing performance.
Conclusion
Bulk bags have come a long way from simple storage sacks. They now represent efficiency, safety, and sustainability. From careful manufacturing by industry leaders like Sudarshan Addpack to smart reuse and environmentally responsible recycling, the journey of a bulk bag is nothing short of remarkable.
For industries that rely on reliable, eco-friendly bulk packaging — the choice of the right bulk bag manufacturers matters. With Sudarshan Addpack, you don’t just get a product. You get a promise — of quality, safety, and a greener tomorrow.
FAQs
1. How long do bulk bags typically last?
Depending on use and quality, bulk bags can last from one trip to several years if reused and stored properly.
2. Are bulk bags safe for food and pharmaceuticals?
Yes, certified food-grade bulk bags follow strict hygiene and material standards to ensure safety.
3. Can damaged bulk bags be repaired and reused?
Minor repairs like patching or re-stitching are possible for multi-use bags, but only if they still meet safety standards.
4. What makes Sudarshan Addpack a top choice among bulk bag manufacturers?
Their commitment to quality, innovation, and sustainability sets them apart in the industry.
5. Are there biodegradable options for bulk bags?
Yes, the industry is moving toward bio-based and biodegradable materials, though they’re still evolving in terms of strength and cost.