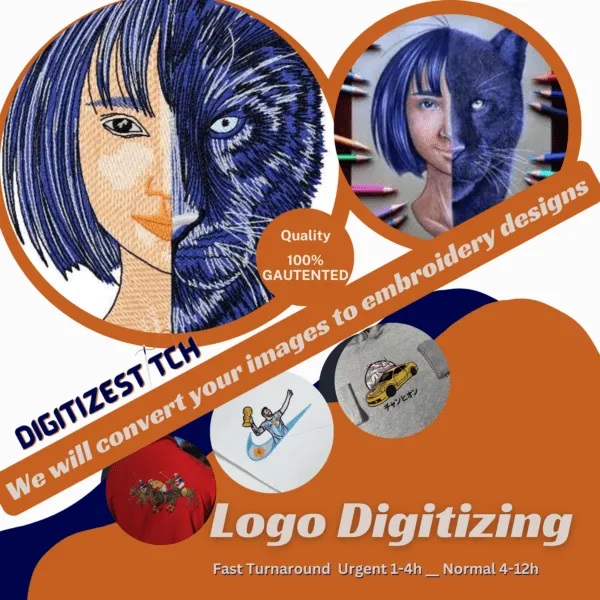
Start With A Super Clear Logo Image
The best way to logo digitizing for embroidery is to begin with a very clear picture of your logo. If you have a paper copy, scan it using a scanner set to high resolution so the lines stay sharp. If your logo is on the computer, save it as a big PNG, PDF, or vector file like AI or EPS. Vector files use points and lines to stay crisp at any size. A clear image helps the software trace every shape accurately and prevents fuzzy edges. When you start with a neat, high-quality logo, the embroidery machine can follow the design exactly. This step sets you up for success before you even open your digitizing software.
Use The Right File Format For Digitizing
Choosing the best file format makes logo digitizing for embroidery easier. Vector files such as AI, EPS, or SVG are ideal because they let you resize without losing clarity. If you don’t have a vector, a large PNG with a transparent background works well too. Avoid small JPEGs that blur when you zoom in. With the right format, the digitizing software can read your logo shapes correctly. After tracing and editing, export your final design in a machine-friendly format like .DST or .PES. Using the correct formats at each step helps your embroidery machine stitch out your logo neatly every time.
Pick The Perfect Size With An Embroidery Size Chart
An embroidery size chart is like a map that shows recommended design sizes for shirt chests, hat fronts, and bag pockets. First, measure the area on your fabric with a ruler. Next, find those numbers on the size chart to see if your logo should be 3 inches or 4 inches wide. Then enter those dimensions into your digitizing software so your design will fit perfectly. A size chart stops mistakes like a design that is too big for a shirt pocket or too small to read. By following the chart, every logo you stitch looks balanced and professional.
Trace Your Logo Shapes Carefully
Once your file is ready and sized, open it in embroidery digitizing software. Use the program’s drawing tools to trace every line and curve of your logo. Zoom in close so you capture small details. Make sure each shape is closed with no gaps, because the machine needs clear outlines to know where to stitch. Take your time tracing so the paths are smooth and accurate. Careful tracing is key to logo digitizing for embroidery and helps the machine make neat, even stitches instead of messy loops or gaps.
Choose The Right Stitch Types
Different parts of your logo need different stitches. Use satin stitches for smooth curving letters or borders, and fill stitches for large color blocks. Running stitches or backstitches work well for thin lines and small details. In your software, select each traced shape and assign the stitch type that fits best. Adjust stitch density so threads aren’t too tight or too loose. Good stitch choices make your design look clear and help it last after many washes. By matching stitch types to your logo shapes, your embroidery will look sharp and professional.
Plan For 3D Puff Embroidery Digitizing
If you want parts of your logo to rise off the fabric, try 3D puff embroidery digitizing. First, decide which letters or shapes will stick up with foam under the stitches. In the digitizing software, mark those areas for foam and set thicker satin stitches to cover the foam completely. Use your embroidery size chart to size the foam parts so they fit inside the hoop. Always test stitching on scrap fabric with foam first. Adjust stitch density and foam thickness until the raised design looks smooth and even. 3D puff makes your logo pop and adds fun texture.
Test Your Design On Scrap Fabric
Before stitching on your final shirt or hat, do a test on scrap fabric with the same stabilizer and hoop size. Load your digitized file into the machine and stitch the design. Check if the size matches your embroidery size chart marks and if stitches lie flat. Look for gaps, loops, or puckering. If something looks off, go back to your software to tweak stitch density, direction, or size. Testing on scrap fabric helps you catch errors early and keeps your final fabric from being wasted. Once your test turns out perfectly, you’re ready to stitch your real project.
Work With Embroidery Digitizing Services USA
If you need help or have a tricky logo, you can hire embroidery digitizing services USA. These experts know how to handle all steps—from reading your size chart to setting up 3D puff areas. You send them your clean logo file and measurements from your embroidery size chart. They return a ready-to-stitch file in the correct format for your machine. Many services include a few free revisions so you can get the design just right. Working with a U.S. service means quick support and clear communication. This makes your digitizing process smooth and worry-free.
Export In The Correct Machine Format
After perfecting your design and passing the test, export the file in the format your embroidery machine uses, such as .DST, .PES, .EXP, or .JEF. In the software, choose “Export” or “Save As” and pick the correct format. Name your file clearly—like “Logo_3in.dst”—so you can find it easily. If you use embroidery digitizing services USA, tell them your machine type before they send the file. Using the right format ensures your machine reads the design correctly and stitches it smoothly without errors.
Hoop, Stitch, And Finish With Care
Finally, hoop your fabric securely with the right stabilizer. Align your hoop so the area you marked with your size chart fits in the center. Load the file into the machine, choose your threads, and press start. Watch the machine as it stitches, fixing any thread breaks or fabric shifts. When stitching ends, remove the hoop and trim loose threads. Peel away or cut off stabilizer, then gently wash out any marking lines. Press your design from the back with a cloth barrier. By hooping, stitching, and finishing carefully, your digitized logo will look neat and strong. It will match the design you created perfectly.