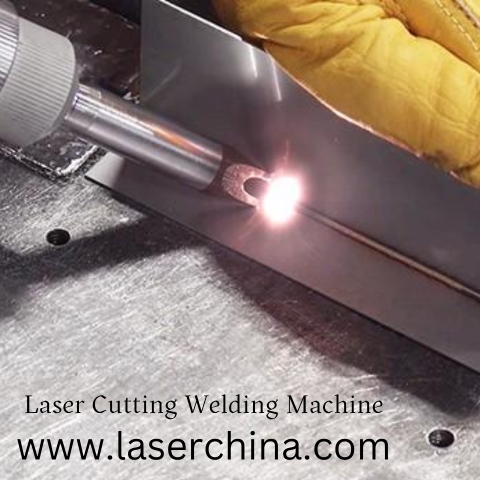
In the fast-evolving world of metal fabrication, the demand for precision, speed, and versatility is higher than ever. Fabricators, manufacturers, and even small workshops are constantly on the lookout for equipment that can do more, with less complexity, and deliver consistent results. One of the groundbreaking innovations serving this demand is the laser cutting welding machine — a hybrid solution that is transforming how we approach metalworking projects.
What is a Laser Cutting Welding Machine?
A laser cutting welding machine is an integrated piece of equipment designed to both cut and weld metals using laser technology. Traditionally, industries would require separate machines for these two functions. Laser cutters were used to make intricate cuts, while laser welders handled the joining of metal components. However, the hybrid version now combines both into one powerful unit.
This dual-functionality means that users can switch between cutting and welding modes effortlessly, optimizing time, space, and cost. By harnessing the concentrated energy of a laser beam, these machines achieve exceptionally fine results, whether slicing through sheets of stainless steel or seamlessly fusing metal parts.
Why the Hybrid Design Matters
You might wonder why combining these two processes into one machine is such a big deal. Here’s the key: workflow efficiency. In a typical manufacturing process, parts often need to be cut before they are welded. Having a single machine perform both operations eliminates the need to transfer parts between different workstations, reducing the chances of errors, misalignments, or contamination.
Additionally, synchronization of cutting and welding operations reduces labor dependency and improves repeatability in high-volume production. This is especially vital in industries like automotive, aerospace, electronics, and custom fabrication — where accuracy is everything.
Industrial Use Cases of Laser Cutting Welding Machines
Across multiple industries, the laser cutting welding machine is finding its place in the spotlight. Let’s dive into some real-world applications:
Automotive Industry
Car manufacturers need to cut and weld thousands of metal components daily. From exhaust systems to chassis frames, the demand for high-speed, accurate, and aesthetically clean welds is non-negotiable. A laser cutting welding machine fits perfectly into this picture, offering seamless transitions between fabrication stages.
Aerospace
The aerospace industry works with complex alloys and high-precision components. The integrated design of this machine helps aerospace engineers maintain tight tolerances, perform detailed cuts, and weld high-strength materials with minimal thermal distortion.
Metal Art & Custom Fabrication
For metal artists and boutique fabricators, the ability to quickly prototype and produce custom parts is a game changer. A laser cutting welding machine allows them to experiment with creative designs, perform intricate detailing, and construct durable welded structures from a single workstation.
Electronics & Enclosures
Electronics often require metal enclosures with ventilation slots, cable channels, and precise fittings. The hybrid machine ensures that every piece is not only cut to exact dimensions but also welded with precision, reducing assembly time and increasing production throughput.
Materials Compatible with Laser Cutting Welding Machines
These machines aren’t limited to a single type of metal. Their versatility allows them to handle a broad spectrum of materials such as:
-
Stainless Steel
-
Carbon Steel
-
Aluminum
-
Titanium
-
Brass
-
Galvanized Sheets
Different materials require different laser settings, but modern systems often come with pre-set modes to simplify the process. This helps both novices and seasoned professionals maintain quality across a variety of jobs.
How it Works: Behind the Scenes
The core mechanism behind a laser cutting welding machine revolves around the power of a focused laser beam, generated by a fiber or CO₂ laser source.
Laser Cutting Mode:
When set to cutting mode, the machine emits a narrow, intense beam that melts, burns, or vaporizes material along a pre-programmed path. Assisted by a high-pressure gas (typically nitrogen or oxygen), the molten material is blown away, resulting in a clean and accurate cut.
Laser Welding Mode:
Switching to welding mode, the laser beam is focused more narrowly to penetrate metal surfaces, allowing them to fuse at the molecular level. Depending on the welding type — whether it’s conduction or keyhole — the machine adjusts the depth and power to ensure strong joints.
The transition between modes is often as simple as switching software presets or changing a nozzle, making the entire process user-friendly.
Common Configurations and Sizes
Laser cutting welding machines come in various configurations based on the type of job you want to handle:
-
Desktop Models: Ideal for small shops or prototyping needs.
-
Benchtop Hybrids: Offer a balance between portability and industrial strength.
-
Industrial Floor Units: Designed for heavy-duty operations with advanced automation, robotic arms, and software integration.
You can also find machines with adjustable working areas (ranging from 300×300 mm up to several meters), and varying power ratings — from 500W for thin sheet work to over 6kW for thick materials.
Software Integration and Smart Controls
Modern laser cutting welding machines are often bundled with intuitive software solutions. These programs allow users to upload designs (via DXF or SVG files), simulate cutting and welding paths, and control machine parameters in real-time. Touchscreens, Wi-Fi connectivity, and remote diagnostics are also becoming standard.
Some systems even feature smart cameras or vision systems for real-time tracking, auto-focus capabilities, and advanced alignment. This means fewer mistakes and greater production quality — all with less manual effort.
Safety Measures and Considerations
While incredibly powerful, these machines are also designed with user safety in mind. Built-in enclosures, emergency stops, and light-shielding mechanisms help protect operators from laser exposure. Still, it’s essential for users to wear proper protective gear, especially laser-rated goggles, and follow recommended safety protocols.
Ventilation systems and fume extractors are also common, particularly when working with materials like galvanized steel, which can release hazardous fumes.
Choosing the Right Laser Cutting Welding Machine
When selecting a laser cutting welding machine, consider the following factors:
-
Type of Work: Are you handling small artistic pieces or large industrial batches?
-
Material Type & Thickness: Make sure the machine’s power rating matches your needs.
-
Precision Requirements: Look for models with stable platforms, high-quality lenses, and motion accuracy.
-
Software Support: Ensure compatibility with CAD/CAM tools you already use.
-
Budget & ROI: While initial investment might be higher, the long-term gains in speed, quality, and labor efficiency often justify the cost.
Also, don’t forget to check for warranty, support services, and the availability of replacement parts when choosing a supplier.
Final Thoughts
The laser cutting welding machine is more than just a piece of equipment — it’s a comprehensive fabrication solution. By merging the two vital processes of metalworking into a single platform, this machine offers unmatched efficiency, precision, and flexibility. Whether you’re producing complex mechanical parts, crafting custom art, or scaling your manufacturing line, investing in this dual-function machine can revolutionize your workflow.
Its adaptability across industries and materials makes it a must-have for anyone serious about modern fabrication. If you’re ready to upgrade your production capabilities and streamline your operations, the laser cutting welding machine is a smart, future-ready choice worth exploring today.