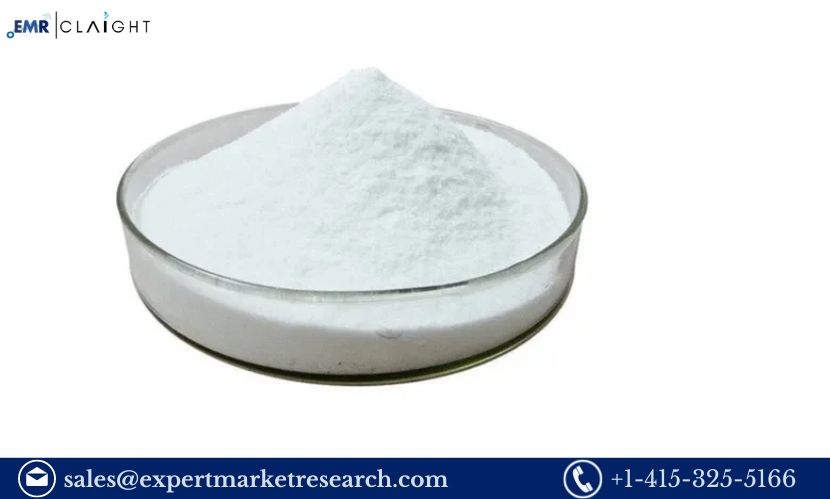
Antifungal powders are crucial in various sectors, including pharmaceuticals, cosmetics, and agriculture, offering effective solutions for fungal infections and growth prevention. As the demand for antifungal products continues to rise, establishing an antifungal powder manufacturing plant can be a lucrative venture. This article serves as a comprehensive Antifungal Powder Manufacturing Plant Project Report, detailing the essential aspects of setting up an antifungal powder manufacturing facility, from conceptualization to operational considerations.
Overview of Antifungal Powders
Antifungal powders are formulated to combat fungal infections and inhibit fungal growth on various surfaces. These powders are commonly used in medical settings to treat conditions such as athlete’s foot, ringworm, and other dermatophyte infections. Additionally, antifungal powders are widely used in agricultural practices to protect crops from fungal diseases, ensuring food security and promoting healthy growth.
Definition of Antifungal Powders
Antifungal powders typically contain active ingredients designed to eliminate or inhibit the growth of fungi. These powders can be classified into various categories based on their application, including topical antifungals for skin infections and systemic antifungals for internal use. The choice of ingredients and formulation depends on the intended use, target market, and regulatory requirements.
Get a Free Sample Report with Table of Contents @
Manufacturing Process of Antifungal Powders
The manufacturing process of antifungal powders involves several key steps that ensure the production of high-quality products. Here’s an overview of the general manufacturing process:
1. Raw Material Selection
The first step in the manufacturing process is the careful selection of raw materials. High-quality active pharmaceutical ingredients (APIs) and excipients must be chosen based on their effectiveness and safety. It is essential to source raw materials from reputable suppliers to ensure consistency and compliance with regulatory standards.
2. Formulation Development
After raw material selection, the formulation development stage begins. This involves determining the optimal combination of active ingredients and excipients to achieve the desired therapeutic effect. Formulation scientists work to create a stable and effective powder, considering factors such as solubility, bioavailability, and release profiles.
3. Mixing and Blending
Once the formulation is finalized, the next step is mixing and blending the raw materials. This is typically done in specialized equipment designed to ensure uniformity in particle size and distribution. Proper mixing is critical to achieving consistent product quality, as uneven blending can lead to variations in potency and efficacy.
4. Milling and Size Reduction
In many cases, the blended powder undergoes milling or size reduction to achieve the desired particle size. This step is crucial, as the particle size can significantly affect the powder’s solubility, absorption, and overall performance. Advanced milling techniques, such as jet milling or ball milling, may be employed to achieve the required specifications.
5. Quality Control and Testing
Quality control is an integral part of the manufacturing process. Each batch of antifungal powder must undergo rigorous testing to ensure it meets safety and efficacy standards. This includes evaluating the purity of raw materials, the potency of active ingredients, and the stability of the final product. Quality assurance measures are implemented to ensure compliance with regulatory requirements.
6. Packaging
Once the antifungal powder passes all quality control tests, it is packaged for distribution. Packaging is a critical aspect, as it must protect the product from moisture, contamination, and degradation. Various packaging materials, such as moisture-resistant bags and bottles, may be utilized based on the product’s specifications and market requirements.
Production Cost Report
Creating a production cost report is vital for assessing the financial feasibility of establishing an antifungal powder manufacturing plant. This report typically includes:
1. Raw Material Costs
A detailed analysis of raw material costs is essential, as these expenses can significantly impact overall production costs. It’s important to account for fluctuations in market prices and consider long-term supplier agreements to mitigate risks.
2. Labor Costs
Labor costs encompass salaries, benefits, and training expenses for the workforce involved in the manufacturing process. Investing in skilled personnel is essential for maintaining high-quality standards and operational efficiency.
3. Equipment and Facility Costs
The costs associated with purchasing or leasing manufacturing equipment and establishing the production facility must be factored into the report. This includes machinery for mixing, milling, and packaging, as well as the costs of utilities and maintenance.
4. Regulatory Compliance Costs
Complying with industry regulations and obtaining necessary certifications can incur additional expenses. It is crucial to allocate funds for regulatory compliance to ensure smooth operations and market access.
5. Marketing and Distribution Costs
Lastly, the report should address marketing and distribution costs to promote the antifungal powders effectively. This may include branding, advertising, and logistics expenses to ensure timely delivery to customers.
Key Considerations for Setting Up an Antifungal Powder Manufacturing Plant
Establishing an antifungal powder manufacturing plant requires careful planning and execution. Here are some critical considerations:
1. Market Research
Conducting thorough market research is essential to understand the demand for antifungal powders, identify target customers, and analyze competitors. This information can guide product development and marketing strategies.
2. Regulatory Compliance
Compliance with industry regulations is paramount for the successful operation of an antifungal powder manufacturing plant. Familiarizing oneself with relevant regulations and obtaining necessary licenses is crucial to avoid legal issues.
3. Location Selection
Choosing the right location for the manufacturing facility is vital. Factors such as proximity to suppliers, distribution networks, and skilled labor should be considered when selecting a site.
4. Technology Adoption
Investing in advanced manufacturing technologies can enhance efficiency, reduce production costs, and improve product quality. Embracing automation and modern equipment can provide a competitive edge in the market.
5. Environmental Considerations
Sustainability and environmental impact are increasingly important in the manufacturing sector. Implementing eco-friendly practices and minimizing waste can enhance the company’s reputation and appeal to environmentally-conscious consumers.
FAQ
What are antifungal powders used for?
Antifungal powders are primarily used to treat fungal infections, prevent fungal growth in crops, and in various cosmetic applications.
How is antifungal powder manufactured?
The manufacturing process involves raw material selection, formulation development, mixing, milling, quality control, and packaging.
What factors affect the cost of producing antifungal powders?
The production cost is influenced by raw material prices, labor costs, equipment expenses, regulatory compliance, and marketing costs.
Is regulatory compliance important in antifungal powder manufacturing?
Yes, compliance with industry regulations ensures product safety, efficacy, and market access, making it essential for successful operations.
How can I ensure the quality of antifungal powders?
Implementing strict quality control measures, conducting regular testing, and sourcing high-quality raw materials can help maintain product quality.
What are the market trends in antifungal powders?
The antifungal powder market is witnessing growth due to increased awareness of fungal infections, advancements in formulation technologies, and a rising demand for effective agricultural solutions.
Related Reports
https://www.expertmarketresearch.com/reports/flexible-plastic-packaging-market
https://www.expertmarketresearch.com/reports/instrument-transformer-market
https://www.expertmarketresearch.com/reports/medium-voltage-motors-market
Media Contact:
Company Name: Claight Corporation
Contact Person: Lewis Fernandas, Corporate Sales Specialist — U.S.A.
Email: [email protected]
Toll Free Number: +1–415–325–5166 | +44–702–402–5790
Address: 30 North Gould Street, Sheridan, WY 82801, USA
Website: www.expertmarketresearch.com
Aus Site: https://www.expertmarketresearch.com.au