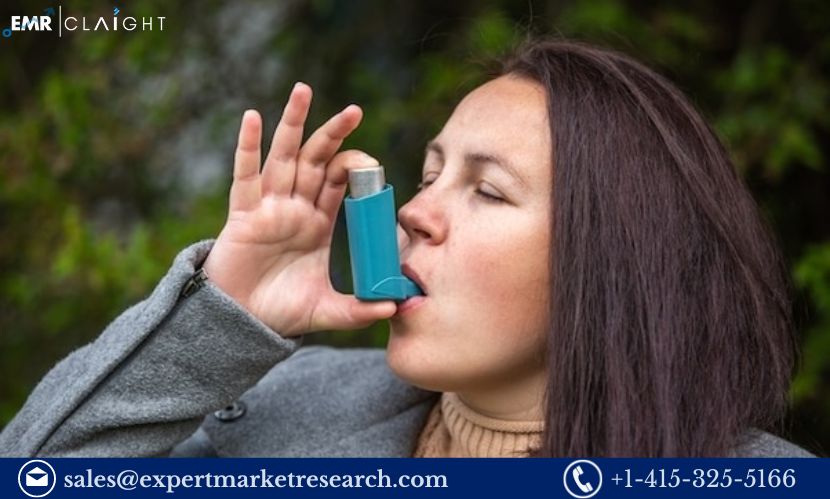
Introduction
Budesonide and formoterol are two essential medications often combined in a single inhaler known as Symbicort. This combination is used to treat asthma and chronic obstructive pulmonary disease (COPD) by providing both anti-inflammatory and bronchodilator effects. The Budesonide or Formoterol (Symbicort) Manufacturing Plant Project report provides a detailed plan for setting up a facility dedicated to producing this critical medication. This article will explore the project’s key elements, including feasibility, benefits, and operational considerations, offering a comprehensive guide to establishing a successful manufacturing plant.
What is Symbicort?
Symbicort is a combination medication that includes:
- Budesonide: A corticosteroid that reduces inflammation in the airways.
- Formoterol: A long-acting beta-agonist that helps relax and open the airways.
Together, these drugs work to manage symptoms of asthma and COPD, improve breathing, and reduce the frequency of exacerbations. Symbicort is typically used via an inhaler, making it an accessible treatment for patients suffering from these chronic respiratory conditions.
Purpose of the Manufacturing Plant
The primary goal of the manufacturing plant is to produce Symbicort in compliance with high-quality standards and regulatory requirements. The plant will focus on:
- Manufacturing Symbicort inhalers with consistent dosage and efficacy.
- Implementing efficient production processes to ensure cost-effectiveness and high product quality.
- Meeting regulatory standards to ensure safety and effectiveness of the medication.
Get a Free Sample Report with Table of Contents @
Key Components of the Project
- Feasibility Study
A feasibility study is essential for assessing the viability of the manufacturing plant. This involves:
- Market Analysis: Evaluating demand for Symbicort and identifying potential competitors.
- Cost Estimates: Analyzing the investment needed for facility construction, equipment, and operational expenses.
- Financial Projections: Projecting revenues, profits, and return on investment.
- Risk Assessment: Identifying potential risks and developing mitigation strategies.
- Regulatory Compliance
Manufacturing pharmaceuticals involves strict adherence to regulatory standards. For Symbicort, this includes:
- FDA Approval: Ensuring compliance with the U.S. Food and Drug Administration (FDA) regulations, including Good Manufacturing Practices (GMP).
- EMA Approval: Meeting European Medicines Agency (EMA) guidelines for manufacturing and quality control.
- Environmental and Safety Regulations: Complying with local environmental laws and ensuring workplace safety.
- Facility Design and Construction
Designing and constructing the plant involves creating a layout that supports efficient and safe production. Key components include:
- Production Areas: Including facilities for blending, filling, and packaging the inhalers.
- Quality Control Laboratories: For testing the drug’s efficacy, safety, and consistency.
- Storage Facilities: For raw materials, intermediate products, and finished inhalers.
- Administrative and Support Spaces: For managing operations, research, and staff.
- Production Process
The production of Symbicort involves several steps:
- Raw Material Sourcing: Procuring high-quality budesonide and formoterol, as well as other excipients required for the inhaler formulation.
- Formulation: Blending budesonide and formoterol with propellants and stabilizers to create the inhalable solution.
- Filling and Assembly: Filling the formulated solution into inhaler canisters and assembling the inhalers.
- Quality Assurance: Conducting rigorous testing to ensure each inhaler meets safety and efficacy standards.
- Packaging: Packaging the inhalers for distribution while maintaining product integrity.
- Quality Control
Quality control is crucial to ensure that Symbicort meets the required standards. This involves:
- Testing for Active Ingredients: Verifying the concentration of budesonide and formoterol in each inhaler.
- Checking Inhaler Functionality: Ensuring that each inhaler delivers the correct dose and functions properly.
- Stability Testing: Assessing the stability of the medication over time under various conditions.
- Market Analysis and Distribution
Effective market analysis helps identify target customers such as pharmacies, hospitals, and healthcare providers. Developing a distribution strategy involves:
- Building Relationships: Establishing partnerships with distributors and healthcare providers.
- Logistics: Ensuring efficient transportation and storage to maintain product quality.
- Marketing Strategies: Implementing marketing campaigns to promote Symbicort and educate healthcare professionals and patients.
Potential Benefits
- Improved Patient Outcomes
By providing a reliable source of Symbicort, the plant can help improve patient outcomes by ensuring consistent availability of this essential medication.
- Economic Growth
The establishment of the manufacturing plant can stimulate local economic growth by creating jobs, attracting investment, and supporting related industries.
- Industry Support
The plant will support the pharmaceutical industry by offering a high-quality product to meet the growing demand for asthma and COPD treatments.
- Innovation and Technology
The project can drive innovation by incorporating advanced manufacturing technologies and processes, leading to improvements in product quality and production efficiency.
Challenges and Risks
- High Investment Costs
Setting up a pharmaceutical manufacturing plant involves significant capital investment. Costs include facility construction, equipment, and regulatory compliance.
- Regulatory Compliance
Navigating the complex regulatory landscape requires meticulous planning and adherence to stringent guidelines, which can be time-consuming and costly.
- Market Competition
The pharmaceutical industry is highly competitive. The plant must differentiate itself through product quality, pricing, and effective distribution strategies.
- Supply Chain Management
Ensuring a consistent supply of high-quality raw materials and managing production logistics can be challenging and requires careful coordination.
FAQ
What is Symbicort used for?
Symbicort is used to manage and treat asthma and chronic obstructive pulmonary disease (COPD). It combines budesonide, an anti-inflammatory corticosteroid, and formoterol, a long-acting bronchodilator, to improve breathing and reduce symptoms.
What are the key steps in the manufacturing process of Symbicort?
The key steps include sourcing raw materials, formulating the medication, filling and assembling inhalers, conducting quality assurance tests, and packaging the finished product.
What are the main regulatory requirements for manufacturing Symbicort?
The plant must comply with regulations from the FDA (for U.S. markets) and EMA (for European markets), including adherence to Good Manufacturing Practices (GMP), environmental laws, and safety regulations.
How can the plant benefit the local economy?
The plant can create jobs, stimulate economic growth, and attract investment. It also supports the local pharmaceutical industry by providing a reliable source of Symbicort.
What challenges might the plant face?
Challenges include managing high investment costs, ensuring regulatory compliance, dealing with market competition, and maintaining a stable supply chain for raw materials.
Media Contact:
Company Name: Claight Corporation
Contact Person: Lewis Fernandas, Corporate Sales Specialist — U.S.A.
Email: [email protected]
Toll Free Number: +1–415–325–5166 | +44–702–402–5790
Address: 30 North Gould Street, Sheridan, WY 82801, USA
Website: www.expertmarketresearch.com
Aus Site: https://www.expertmarketresearch.com.au