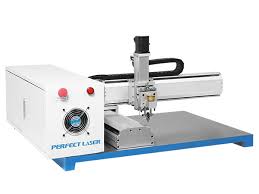
A laser glass cutting machine operates with remarkable accuracy, offering a contact-free method of shaping and engraving glass. Unlike traditional cutting methods that rely on physical blades or abrasive tools, a laser system uses concentrated light energy to create precise cuts. This raises an intriguing question: can a laser cut glass without making physical contact? The answer lies in understanding how laser technology interacts with glass surfaces.
How a Laser Glass Cutting Machine Works
A laser glass cutting machine utilizes a high-intensity laser beam that targets specific areas on the glass surface. This focused energy generates heat, leading to controlled fractures along designated paths. The absence of direct mechanical force distinguishes it from conventional cutting techniques.
The process involves:
- Laser Focusing: The beam is directed onto the glass, creating a localized heating effect.
- Thermal Stress Induction: The rapid temperature change causes expansion and contraction in the material, leading to a controlled fracture.
- Guided Breakage: A cooling agent, such as air or water, helps guide the break along the intended cutting line.
Since there is no physical blade involved, the laser never physically “touches” the glass. However, the energy from the laser interacts with the material at a microscopic level, making it a unique, contact-free cutting method.
Understanding the Interaction Between Laser and Glass
The effectiveness of a laser glass cutting machine depends on factors like laser wavelength, power intensity, and glass composition. Certain types of glass, such as tempered glass, may respond differently to laser cutting due to their internal stress patterns.
- Wavelength Selection – Infrared lasers are commonly used for glass cutting because they efficiently absorb energy.
- Power Control – Adjusting the laser’s power ensures clean, precise cuts without unwanted thermal damage.
- Glass Type Consideration – Borosilicate, soda-lime, and quartz glass all have distinct reactions to laser energy.
Even though the laser doesn’t make physical contact, its high-energy beam alters the glass at a molecular level, enabling precise cutting without traditional tools.
Comparing Traditional and Laser-Based Glass Cutting
Traditional glass cutting relies on mechanical tools such as diamond-tipped cutters or water jet systems. These methods require direct contact and exert physical pressure to create fractures. A laser glass cutting machine, on the other hand, eliminates mechanical wear and tear, offering a cleaner and more efficient alternative.
Aspect | Traditional Cutting | Laser Glass Cutting Machine |
---|---|---|
Contact with Glass | Physical blade or cutter | No physical contact, only laser energy |
Precision Level | Moderate to high | Extremely high |
Maintenance Required | Regular blade replacement | Minimal maintenance |
Edge Quality | May require post-processing | Smooth and clean cuts |
This comparison highlights the advantages of laser-based cutting techniques, emphasizing the efficiency of a non-contact approach.
Common Applications of Laser Glass Cutting
A laser glass cutting machine is widely used in industries that require precision and intricate detailing. Some common applications include:
- Electronics Industry – Used for cutting smartphone screens, LCD panels, and optical components.
- Automotive Sector – Helps in shaping car windows and windshields with high accuracy.
- Decorative and Architectural Glass – Used for engraving patterns and cutting intricate shapes for interior design.
- Medical Equipment – Assists in manufacturing glass components for laboratory and diagnostic devices.
Each of these applications benefits from the machine’s ability to cut glass without physical contact, reducing risks associated with material stress and breakage.
Factors That Influence Laser Glass Cutting Performance
When using a laser glass cutting machine, several factors play a crucial role in determining the quality of the cut:
- Laser Beam Quality: The coherence and focus of the laser affect the precision of the cutting process.
- Glass Thickness: Thinner glass generally requires lower power, while thicker glass needs controlled power settings to prevent overheating.
- Speed and Feed Rate: A slower speed can enhance precision, while a higher speed may improve production efficiency.
- Cooling and Support Systems: Using water or air cooling prevents unwanted thermal stress and improves the cutting process.
Optimizing these factors ensures that the laser delivers consistent and high-quality cuts without causing unnecessary material damage.
Myths and Misconceptions About Laser Glass Cutting
Since a laser glass cutting machine operates without direct contact, there are several misconceptions about its capabilities:
- Myth: Laser cutting burns through glass like it does with metal.
- Reality: Glass doesn’t burn; instead, it undergoes controlled fracturing due to thermal stress.
- Myth: All types of glass can be cut with a laser.
- Reality: While many types of glass respond well, tempered glass is difficult to cut due to its internal stress structure.
- Myth: A laser cuts glass instantly.
- Reality: The process requires precise adjustments in speed, power, and cooling to ensure clean cuts.
Understanding these distinctions helps in choosing the right laser settings for specific cutting tasks.
Conclusion
A laser glass cutting machine provides a precise and non-contact method for shaping glass. While the laser never physically touches the material, its concentrated energy induces thermal stress, leading to controlled fractures. This innovative approach makes it an essential tool in industries that demand high-precision glass cutting.
By leveraging the capabilities of a laser glass cutting machine, manufacturers can achieve cleaner cuts, minimal material waste, and enhanced efficiency. The ability to cut glass without physical contact showcases the power of laser technology, revolutionizing modern glass processing techniques.