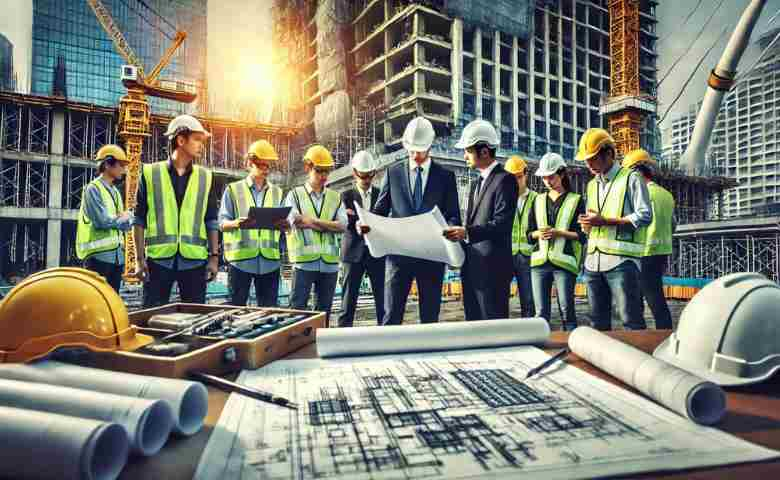
Construction quality management is an essential aspect of ensuring safe, durable, and cost-effective infrastructure. However, maintaining high-quality standards in construction projects comes with numerous challenges. Issues such as poor workmanship, inadequate materials, lack of skilled labor, and regulatory compliance difficulties can hinder project success. This article explores common challenges in construction quality management and provides effective strategies to overcome them.
1. Poor Workmanship
Challenge
One of the most prevalent issues in construction consulting firms quality management is poor workmanship. This can result from insufficient training, lack of supervision, or rushed project schedules. Poor workmanship leads to structural defects, rework, and increased costs.
Solution
To overcome this challenge, companies should invest in continuous training programs for workers and supervisors. Implementing strict quality control measures, including regular site inspections and performance assessments, can help maintain high workmanship standards. Utilizing advanced construction technologies, such as Building Information Modeling (BIM), can also aid in improving precision and reducing errors.
2. Use of Low-Quality Materials
Challenge
The use of substandard materials compromises the safety and longevity of construction projects. Contractors may opt for cheaper materials to cut costs, but this often results in project failures and increased maintenance expenses.
Solution
Strict procurement policies should be enforced to ensure high-quality materials are used. Contractors must work with reputable suppliers and conduct rigorous material testing before use. Establishing quality benchmarks and ensuring compliance with industry standards will also mitigate the risks associated with low-quality materials.
3. Lack of Skilled Labor
Challenge
A shortage of skilled labor is a major challenge in the construction industry. Many projects suffer from delays and poor execution due to a lack of experienced workers.
Solution
Companies should focus on attracting and retaining skilled labor through competitive wages, benefits, and career development opportunities. Partnering with vocational training institutions and implementing apprenticeship programs can help bridge the skills gap. Additionally, embracing automation and robotics can supplement human labor and improve efficiency.
4. Inefficient Quality Control Processes
Challenge
Manual quality control processes are often slow, prone to human error, and inefficient in identifying defects early in construction projects.
Solution
Adopting digital quality management systems can streamline inspections and documentation. Tools such as drones for site inspections, AI-driven quality assessment software, and real-time data analytics can enhance accuracy and efficiency. Implementing standardized protocols and regular audits ensures that quality standards are consistently met.
5. Compliance with Regulatory Standards
Challenge
Navigating the complex landscape of building codes, safety regulations, and environmental laws can be overwhelming. Failure to comply can result in legal penalties, project shutdowns, and reputational damage.
Solution
Hiring compliance experts and legal advisors can help ensure adherence to all relevant regulations. Regular training on regulatory updates for project managers and workers is essential. Implementing automated compliance tracking systems can also help manage documentation and regulatory submissions more effectively.
6. Cost Overruns Due to Rework
Challenge
Rework due to quality issues can significantly increase project costs and timelines. Construction defects often arise from miscommunication, poor planning, and inadequate quality checks.
Solution
Preventative measures such as conducting thorough pre-construction planning, using detailed blueprints, and ensuring clear communication among stakeholders can reduce the need for rework. Implementing Lean construction principles, which focus on eliminating waste and enhancing efficiency, can also help minimize cost overruns.
7. Inconsistent Communication and Coordination
Challenge
Poor communication and lack of coordination between project teams, contractors, and suppliers can lead to misunderstandings, delays, and quality issues.
Solution
Using collaborative project management software, such as Procore, PlanGrid, or BIM 360, can facilitate real-time communication and document sharing. Establishing a clear chain of command and holding regular coordination meetings ensures that everyone is aligned with the project’s quality expectations.
8. Project Delays Affecting Quality
Challenge
Delays in project timelines can pressure teams to rush work, leading to compromised quality. Factors such as adverse weather, supply chain disruptions, and unforeseen site conditions contribute to project delays.
Solution
Developing a realistic project timeline with contingency plans for potential disruptions is essential. Utilizing project scheduling software and risk assessment tools can help anticipate delays and provide alternative solutions. Strong supplier relationships and a well-organized procurement strategy can also ensure timely material availability.
9. Safety Issues Impacting Quality
Challenge
Safety and quality go hand in hand in construction. Unsafe working conditions can result in accidents that compromise project quality and worker well-being.
Solution
Implementing a robust safety management system, including regular safety training, proper use of personal protective equipment (PPE), and routine safety audits, can mitigate risks. Encouraging a safety-first culture ensures that workers adhere to best practices, ultimately enhancing overall project quality.
Conclusion
Construction quality management faces numerous challenges, from poor workmanship and substandard materials to regulatory compliance and project delays. However, by implementing effective training programs, adopting advanced technology, enforcing strict quality control measures, and fostering collaboration, these challenges can be successfully overcome. A proactive approach to quality management not only ensures the longevity and safety of construction projects but also enhances efficiency and profitability for all stakeholders involved.