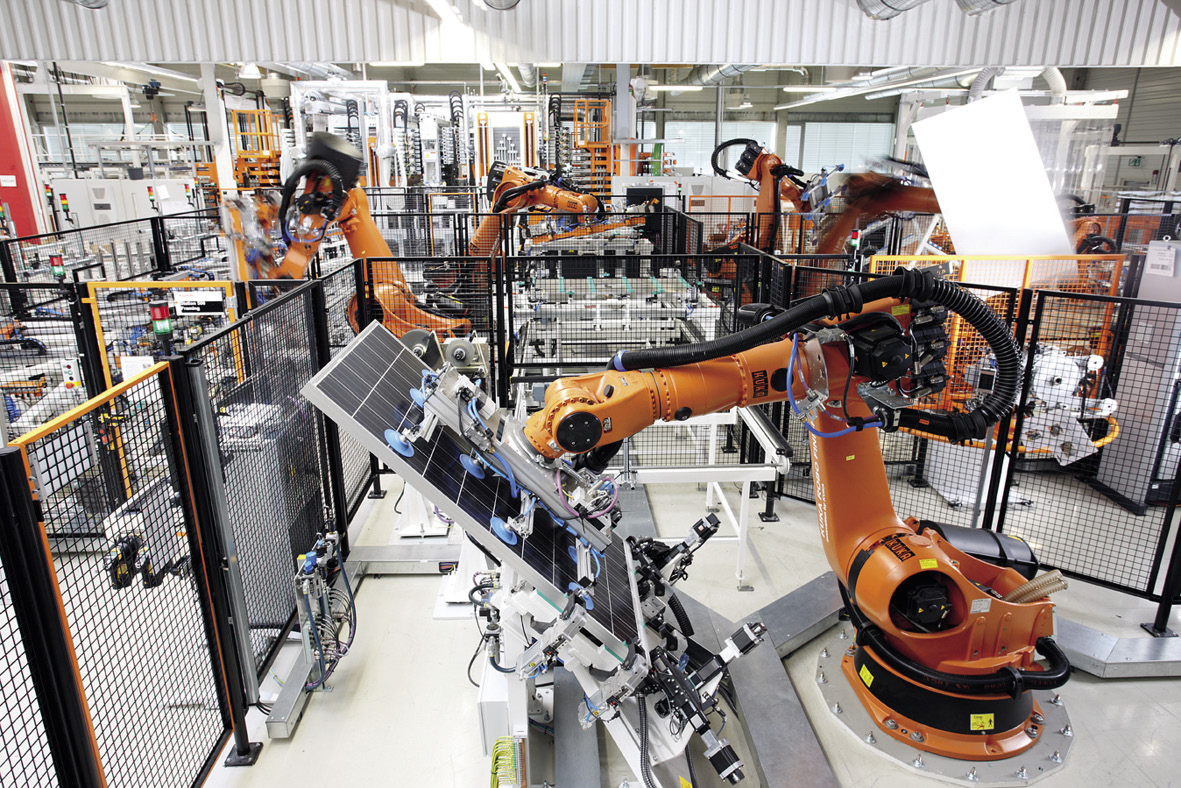
Assembly line systems have come a long way, evolving to meet the diverse needs of modern manufacturing. Customising these systems to fit specific production requirements is crucial for achieving optimal efficiency and flexibility. In this article, we’ll explore the various ways you can tailor assembly line systems to suit your unique production needs.
Understanding Your Production Requirements
Assessing Current Capabilities
Before customising your assembly line, it’s essential to assess your current capabilities. Identify the strengths and weaknesses of your existing system and determine what improvements are needed to meet your production goals.
Defining Your Goals
Clearly define your production goals. Whether it’s increasing output, improving quality, or reducing costs, having well-defined objectives will guide your customisation efforts.
Incorporating Flexibility into Your Assembly Line
Modular Design
A modular design allows for easy reconfiguration of the assembly line. This flexibility is crucial for adapting to changes in product design or production volume. By using interchangeable modules, you can quickly adjust your system to meet new requirements.
Scalability
Ensure that your assembly line system is scalable. As your business grows, your production needs will change. A scalable system can accommodate increased production without significant downtime or additional investment.
Leveraging Advanced Technologies
Automation and Robotics
Integrating automation and robotics can significantly enhance efficiency and precision. Automated systems can handle repetitive tasks, reducing human error and increasing production speed. Robotics can also perform complex operations that require high accuracy.
Artificial Intelligence and Machine Learning
AI and machine learning technologies can optimise your assembly line by predicting maintenance needs, identifying inefficiencies, and suggesting improvements. These technologies enable data-driven decision-making, enhancing overall productivity.
Customising for Specific Products
Tailored Workstations
Design workstations that cater specifically to your products. This includes custom fixtures, tools, and equipment that ensure each task is performed accurately and efficiently. Tailored workstations can reduce setup time and improve product quality.
Product-Specific Software
Utilise software solutions designed for your specific products. Custom software can streamline operations, from inventory management to quality control, ensuring that your assembly line runs smoothly and efficiently.
Enhancing Quality Control
Automated Inspection Systems
Incorporate automated inspection systems to maintain high-quality standards. These systems use advanced imaging and sensors to detect defects, ensuring that only top-quality products move forward in the production process.
Real-Time Monitoring
Implement real-time monitoring to track the performance of your assembly line. This allows you to quickly identify and address any issues, maintaining consistent product quality and reducing downtime.
Ensuring Cost-Effectiveness
Energy Efficiency
Invest in energy-efficient machinery and practices. This not only reduces operational costs but also aligns with sustainable manufacturing goals. Energy-efficient systems can significantly lower your overall expenses.
Optimising Resource Utilisation
Optimise the use of resources, including materials, labour, and time. Efficient resource management reduces waste and enhances productivity, contributing to a more cost-effective assembly line.
Implementing Lean Manufacturing Principles
Eliminating Waste
Lean manufacturing focuses on eliminating waste in all forms, from excess inventory to inefficient processes. By incorporating lean principles, you can streamline your assembly line, reduce costs, and improve efficiency.
Continuous Improvement
Foster a culture of continuous improvement. Regularly assess your assembly line processes and implement changes that enhance productivity and quality. Continuous improvement ensures that your system remains efficient and effective over time.
Training and Development
Skilled Workforce
Invest in training and development for your workforce. Skilled employees are crucial for operating and maintaining customised assembly line systems. Regular training ensures that your team can effectively manage advanced technologies and processes.
Collaborative Training Programs
Develop collaborative training programs that involve both management and frontline workers. This inclusive approach ensures that everyone is on the same page, fostering a culture of teamwork and efficiency.
Future-Proofing Your Assembly Line
Adapting to Technological Advances
Stay abreast of technological advances in assembly line systems. Regularly update your system with the latest innovations to maintain a competitive edge. Future-proofing your assembly line ensures long-term efficiency and productivity.
Planning for Growth
Plan for future growth by designing an assembly line that can easily adapt to increased production demands. Scalability and flexibility are key components of a future-proof system, enabling your business to grow without major disruptions.
Conclusion
Customising assembly line systems to fit your production needs is essential for achieving maximum efficiency and productivity. By incorporating flexibility, leveraging advanced technologies, and focusing on quality control, you can create a tailored system that meets your unique requirements. Embrace lean manufacturing principles, invest in workforce training, and plan for future growth to ensure long-term success.