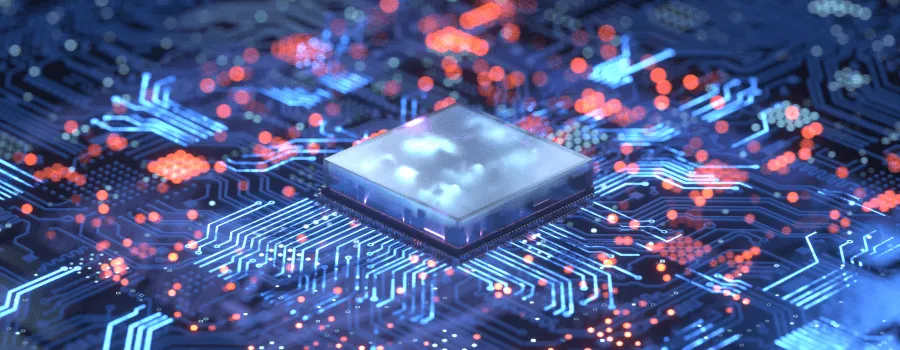
In the rapidly evolving world of technology, the journey from concept to reality is filled with numerous challenges and opportunities. At Jenex Technovation, based in Ahmedabad, India, we specialize in providing cutting-edge embedded hardware solutions that turn innovative ideas into functional products. This article explores how embedded hardware solutions play a crucial role in bridging the gap between conceptualization and tangible, operational systems.
The Role of Embedded Hardware Solutions
Embedded hardware solutions form the backbone of modern electronic devices, enabling them to perform specific tasks efficiently and reliably. These solutions encompass various components such as microcontrollers, sensors, actuators, connectivity modules, power management systems, and human-machine interfaces. Together, they create a cohesive system that can interact with the physical world, process data, and execute commands.
Microcontrollers and Microprocessors
At the heart of any embedded system lies the microcontroller (MCU) or microprocessor. These are the “brains” of the operation, executing instructions, processing data, and controlling other components.
Key Considerations:
- Processing Power: The choice between MCUs and microprocessors depends on the processing needs. MCUs like ARM Cortex-M series are suitable for low-power, high-efficiency tasks, while microprocessors like ARM Cortex-A series are ideal for more computationally intensive applications.
- Memory Requirements: Adequate RAM and flash memory are crucial for running applications smoothly. Projects with large codebases or requiring high-speed data processing need more memory.
- Peripheral Support: Ensure the chosen MCU or microprocessor supports necessary peripherals such as ADCs, DACs, PWM, UART, SPI, and I2C for seamless integration with other components.
Sensors and Actuators
Sensors gather data from the environment, and actuators carry out actions based on processed information. These components are essential for creating responsive and adaptive systems.
Key Considerations:
- Type and Precision: The type of sensor needed depends on the application, whether it’s temperature, humidity, motion, or pressure sensors. Precision and accuracy are paramount for reliable data collection.
- Integration: Ensure sensors and actuators are compatible with the chosen MCU or microprocessor. Wireless sensors add flexibility and reduce wiring complexity, which is advantageous in many applications.
Connectivity Modules
Connectivity is vital for communication between devices and central control systems. It enables data exchange, remote monitoring, and control.
Key Considerations:
- Type of Connectivity: Choose based on the range and data rate required. Wi-Fi and Bluetooth are common for short-range communication, while LoRa and cellular modules are suitable for long-range communication.
- Power Consumption: Wireless modules should be energy-efficient to prolong battery life in portable devices.
Power Management Systems
Efficient power management is crucial for the longevity and reliability of embedded systems, especially those operating in battery-powered environments.
Key Considerations:
- Voltage Regulation: Ensure stable voltage supply to all components to prevent damage and ensure consistent performance.
- Battery Management: Advanced battery management systems (BMS) are essential for monitoring and optimizing battery health and longevity.
- Energy Efficiency: Low-power MCUs and energy harvesting techniques can significantly extend battery life and reduce operational costs.
Human-Machine Interfaces (HMIs)
HMIs facilitate interaction between users and machines, providing essential feedback and control capabilities.
Key Considerations:
- Usability: HMIs should be intuitive and user-friendly to enhance user experience and reduce training time.
- Durability: For industrial applications, HMIs should be robust and capable of withstanding harsh environmental conditions.
- Remote Accessibility: Cloud-connected HMIs enable remote monitoring and control, enhancing flexibility and responsiveness.
Security Solutions
Security is a paramount concern in embedded systems, particularly with the rise of IoT devices susceptible to cyber threats.
Key Considerations:
- Encryption: Data should be encrypted both at rest and in transit to prevent unauthorized access.
- Authentication: Robust authentication mechanisms ensure only authorized users can access and control the system.
- Secure Boot: Implementing secure boot processes ensures that only trusted firmware is executed, protecting against malware and unauthorized modifications.
The Journey from Concept to Reality
Conceptualization and Design
The first step in any embedded project is conceptualization and design. This involves understanding the project’s requirements, defining the system’s architecture, and selecting appropriate hardware components.
Steps Involved:
- Requirement Analysis: Understand the functional, performance, and environmental requirements of the project.
- System Architecture: Define the overall architecture, including the selection of MCUs, sensors, actuators, connectivity modules, and power management systems.
- Component Selection: Choose components based on the defined requirements, ensuring compatibility and scalability.
Prototyping and Development
Prototyping is a critical phase where the concept is transformed into a tangible product. It involves developing a working model of the system to test its feasibility and performance.
Steps Involved:
- Development Boards: Use development boards like Arduino, Raspberry Pi, or custom-designed PCBs to create a prototype.
- Firmware Development: Write and test firmware to control the hardware components and implement the required functionalities.
- Integration Testing: Ensure all components work together seamlessly, identifying and resolving any issues.
Testing and Validation
Thorough testing and validation are essential to ensure the system meets all requirements and performs reliably under various conditions.
Steps Involved:
- Functional Testing: Verify that the system performs all intended functions correctly.
- Performance Testing: Assess the system’s performance, including speed, responsiveness, and power consumption.
- Environmental Testing: Test the system’s resilience to environmental factors such as temperature, humidity, and vibration.
- Compliance Testing: Ensure the system complies with relevant industry standards and regulations.
Production and Deployment
Once the system has been thoroughly tested and validated, it can move into production and deployment. This phase involves scaling up from a prototype to mass production and deploying the system in its intended environment.
Steps Involved:
- Manufacturing: Work with manufacturing partners to produce the hardware components in volume.
- Quality Control: Implement stringent quality control measures to ensure each unit meets the required standards.
- Deployment: Install and configure the system in its operational environment, providing necessary training and support to users.
Maintenance and Updates
The journey doesn’t end with deployment. Ongoing maintenance and updates are crucial to ensure the system continues to perform optimally and remains secure.
Steps Involved:
- Regular Maintenance: Perform routine maintenance to address wear and tear and ensure continued performance.
- Firmware Updates: Provide regular firmware updates to add new features, fix bugs, and address security vulnerabilities.
- Monitoring and Support: Implement remote monitoring and support to quickly identify and resolve any issues.
Conclusion
Embedded hardware solutions are essential in transforming innovative concepts into functional, reliable products. At Jenex Technovation , we provide comprehensive embedded services that guide you through every stage of this journey, from conceptualization and design to production and maintenance.
By carefully selecting the right components, thoroughly testing and validating the system, and providing ongoing support, we ensure that your embedded project not only meets but exceeds expectations. Whether you’re developing an IoT device, an industrial automation system, or any other embedded application, our expertise and commitment to excellence can help you bridge the gap between concept and reality. Contact us today to learn more about how we can support your embedded hardware needs and bring your vision to life.