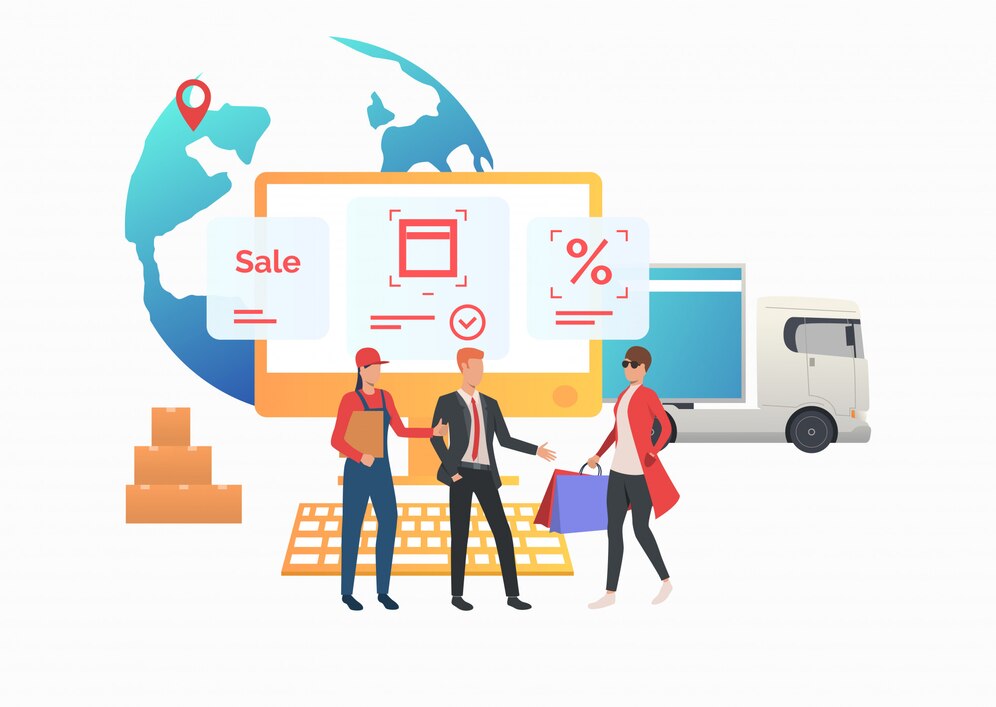
In an economy that is both highly competitive and service-intensive, responsiveness and efficiency are essential differentiators for field service operations. Wherever they work — on medical equipment, HVAC units, or telecommunications infrastructure — technicians have to be ready to go to customer sites with the proper tools, parts, and materials. That’s where Trunk Inventory Management is not only a valuable tool but an imperative strategy.
Field Service Optimization via Clever Trunk Inventory Solutions is at the forefront of revolutionizing the way businesses handle field inventory. Through real-time monitoring, cloud platforms, and automations, this solution enables organizations to lower their costs, boost productivity, and enhance customer satisfaction.
What is Trunk Inventory Management?
Trunk Inventory Management is the inventory tracking, control, and replenishment of parts and materials carried in the trunks or vehicles of field service technicians. Manually, these inventories have traditionally been dealt with, resulting in inaccuracies, stockouts, overstocking, and wasted technician time.
Today’s solutions, like Field Service Optimization Through Smart Trunk Inventory Solutions, allow businesses to track trunk stock in real time, automate replenishment, and make inventory information mobile for technicians. This guarantees that they have the right parts on hand when and where they are needed.
Why Trunk Inventory Matters More Than Ever
As customer expectations continue to grow and same-day service becomes the new standard, first-visit completions by technicians are essential. Research indicates first-time fix rates are among the best predictors of customer satisfaction with field services. Poor inventory levels are among the leading causes of unsuccessful service calls.
Here’s how poor trunk inventory affects business:
More return visits and increased resolution times
Reduced technician productivity from unplanned warehouse trips
Customer frustration with delays or less-than-complete service
Revenue loss from lost service opportunities
Through smart trunk inventory management, companies can remove these inefficiencies and make their field operations a streamlined, responsive, and cost-saving engine of growth.
1. Real-Time Inventory Visibility
With intelligent trunk inventory solutions, managers have real-time visibility into the inventory levels of each field technician’s truck. This enables instant decisions, right-stocking inventory, and minimized downtime. Technicians can even verify part availability across departments, reducing duplicate inventory and maximizing utilization.
2. Automated Replenishment
Automated restocking ensures every technician’s trunk is refilled according to actual consumption and minimum levels. This saves guesswork and manual monitoring commonly associated with restocking, enhancing precision and minimizing the possibility of stockouts.
Field Service Optimization With Intelligent Trunk Inventory Solutions provides intelligent reordering based on past consumption data, job types, and geographic demand — making inventory smarter, not necessarily faster.
3. Mobile Access for Technicians
Field technicians are also able to access their inventory information on mobile devices, with less dependence on office communication and greater autonomy. They can record usage, request transfers, or borrow parts from coworkers nearby — all on their smartphone or tablet.
This independence not only provides improved response times but also enables technicians to provide greater customer service.
4. Lower Shrinkage and Loss
Manual systems tend to result in lost parts or unrecorded inventory loss. Smart trunk inventory systems monitor all movement of parts, establishing an open chain of custody. With barcode or RFID integration, companies can avoid loss, hold employees accountable, and achieve audit-ready inventory records.
5. Smooth Integration with ERP and Field Service Management Software
For optimal operational impact, trunk inventory must not exist in a silo. Products such as Field Service Optimization Through Smart Trunk Inventory Solutions blend with current ERP, CRM, and field service management systems — keeping inventory aligned with job assignment, billing, and reporting.
Business Impact: The ROI of Smart Trunk Inventory
Trunk inventory management solutions are commonly adopted by companies that experience instantaneous performance improvements across metrics such as:
20–30% lift in first-time fix rates
Up to 40% cut in inventory carrying costs
Quicker job resolution and reduced rescheduled visits
Enhanced technician satisfaction and reduced turnover
Higher customer retention and service revenue
Essentially, better inventory translates to better business results.
Who Can Benefit?
Intelligent trunk inventory solutions are especially beneficial for: ‘
Medical equipment service companies
HVAC and plumbing contractors
Telecom and cable installation crews
Utility and infrastructure maintenance companies
Any mobile workforce that handles high-value or time-sensitive inventory
Looking Ahead: The Future of Trunk Inventory
As field service advances, the future of trunk inventory management is one of increasingly automated and intelligent solutions. Predictive analytics, AI-powered inventory planning, and IoT-capable inventory sensors are on the horizon — and companies that jump into these advancements early will achieve a significant competitive advantage.
Final Thoughts
In 2025 and beyond, operational agility and resource availability will be crucial to field service excellence. Trunk Inventory Management is no longer a back-office issue — it is a frontline strategy. With Cloud-in-Hand® Solutions Platform companies can make sure their technicians are always ready, their customers are always happy, and their operations are always optimized.