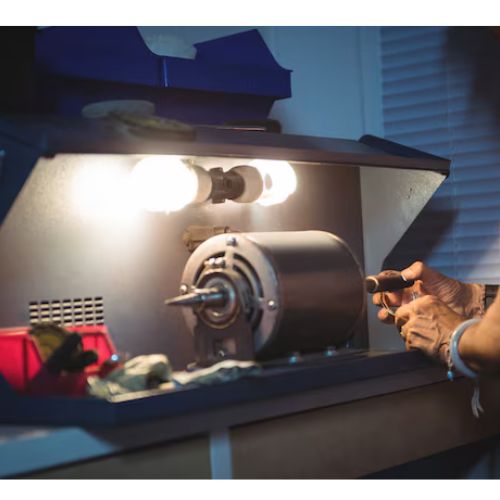
Precision has lost its status as a luxury and has become merely the minimum standard in today’s competitive manufacturing environment. With increasing material costs and ever-stricter tolerances for production, manufacturers need strategies that will help cut waste without compromising on any measure of output.
CNC laser calibration in Pennsylvania is a neglected but important method where high-precision methods are used for machine performance improvement and consistency of product output. It has been a quiet companion within lean production facilities and has become foundational in the quest to reduce material waste in CNC operations.
The Imperative of Accuracy in CNC Machining
Advanced CNC machines run under close tolerances, frequently in microns. Yet small misalignments or mechanical drifts can cause substantial material waste over time. Calibration keeps machine axes on their targeted paths, minimizing deviations that degrade part quality. In production runs with high volume, uncalibrated machinery can produce hundreds of defective components before the issue is caught, each a lost investment in time, material, and labor.
CNC laser calibration employs interferometric or laser tracker systems to measure machine positioning and geometry with high accuracy. Identifying and correcting minor displacements in machine travel invisible to the naked eye is essential since these will affect the product quality. By periodically calibrating machines, manufacturers can keep their tolerances tighter and require less rework and a lower scrap rate.
The Role of CNC Laser Calibration and Alignment in Quality Control
Laser alignment is an essential calibration process that aligns all mechanical parts into their correct orientation. Spindle, bed, or axis misalignment causes geometric errors in the cutting or drilling process, causing cumulative errors for large production batches. A minor angular deviation,n even over a short period, can be magnified to substantial dimensional defects.
When laser tools align machines to a precise degree, they cut or shape materials precisely as instructed. This results in less material being over-cut or under-processed and fewer parts outside spec. Therefore, alignment is critical, especially in industries such as aerospace or medical device manufacturing, wherein even minor deviations may cause stringent regulations.
How CNC Laser Calibration Intersects with Lean Manufacturing
Lean manufacturing strives to eradicate waste in every form—time, energy, motion, and material. In such a paradigm, machine tool calibration is not an isolated remedy but a preventive, planned activity inherent in continuous improvement paradigms. Just-in-time production, for example, relies on dependable machine action. Any discrepancy from anticipated outputs can interrupt supply chains and inventory levels.
Machine calibration also plays a role in standardization. With all machines within a facility performing at maximum accuracy, process variability is reduced. This consistency allows for consistent part quality over multiple shifts and operators. This minimizes inspection over time, decreases production cycles, and builds confidence between manufacturers and customers.
The Cost of CNC Laser Calibration vs. The Cost of Waste
There is a false perception that laser calibration is too costly or time-consuming for routine application. The actual cost is in what’s wasted when equipment isn’t calibrated. Material waste from inefficient cuts can add up to thousands of dollars over weeks or months. The return on the investment for calibration becomes visible when accounting for the cost of rework, labor, machine downtime, and reputational risk.
A calibrated CNC machine uses relatively few raw materials per part finished, extends tool life through reduced cutting stress from uneven load distributions, and saves energy as a result of streamlining motion paths. Altogether, these savings often exceed the cost of routine CNC laser calibrations in Pennsylvania, making it a reasonable practice in terms of long-term economic viability and profitability for facilities interested in being around for the long haul.
Advancing Sustainability Through Precision
Manufacturing sustainability extends beyond simply employing green materials. It includes making wiser choices that avoid waste and reduce consumption at its source. It is a zero-emission and cost-friendly environmental practice, CNC laser calibration-powered precision engineering. The businesses reduce wastes that go to landfills and conserve resources, such as metals found in production and other plastic and composites, through no overproduction as well as no material waste.
Moreover, laser-calibrated machines are also said to run more efficiently with less power consumption and reduced chances of breakdowns.. This results in reduced waste related to maintenance, such as obsolete parts, lubricants, and tools. Sustainability is thus a natural byproduct of operating excellence.
Creating a Culture of CNC Laser Calibration
The Involved Calibration Needs to Be Part of a Bigger Quality Culture That Exists in the Manufacturing Environment. Operators, Engineers, and Maintenance People Must Be Trained to Early Recognize Misalignments or Drift. Digital Tracking Systems Can Be Programmed to Record Calibration Intervals and Generate Future Maintenance Automated Reminders.
Daily CNC laser alignment and machine tool calibration not only enhance precision; they contribute to creating awareness of performance and accountability across teams. If calibration is made a team effort and not a technician’s activity, it enhances the entire value chain from setup to inspection.
A Nutshell: Precision Over Waste:
The advances in programming and tooling that improve CNC waste reduction also include accuracy at the machine level. CNC laser calibration in Pennsylvania is a well-established means by which one would achieve such accuracy necessary in lean and sustainable manufacturing.
Alignment and routine machine tool calibration ensure quality parts production, lower rework, and less raw material consumption. This makes calibration not just a process of maintenance in a cost and performance-oriented business but also a pathway toward competitive edge.