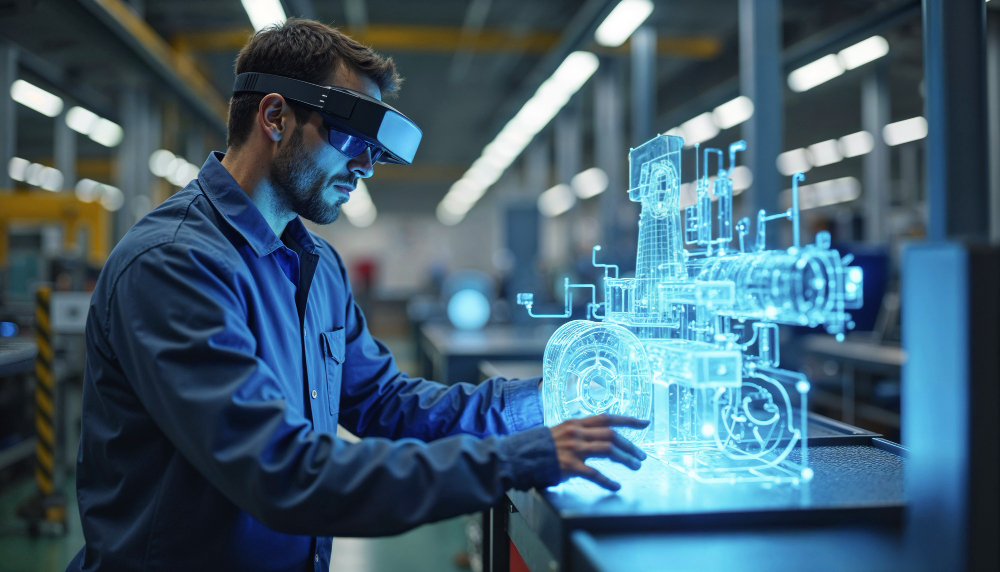
As manufacturing operations become increasingly complex, ensuring worker safety and achieving high levels of precision are critical objectives for factory managers and engineers. Traditional methods often rely on extensive documentation, verbal instructions, and manual training, which may not always translate to consistent execution on the shop floor. Emerging technologies now offer new ways to address these challenges with greater efficiency.
One of the most promising innovations is enhanced AR in manufacturing. By overlaying real-time digital information onto physical environments, augmented reality (AR) empowers workers with contextual data, visual instructions, and guided procedures. This approach not only improves task accuracy but also plays a vital role in reducing safety incidents, especially in high-risk environments.
Enhancing Safety Protocols on the Factory Floor
AR tools can significantly improve the visibility of hazards and guide safe behavior in real time.
-
Workers receive immediate visual alerts for dangerous areas, hot surfaces, or moving machinery.
-
Safety checklists and standard operating procedures can be displayed through AR headsets, reducing the chance of missed steps.
-
Emergency response training becomes more engaging and effective through AR simulations.
Increasing Accuracy in Assembly and Inspection Tasks
Manufacturing precision often depends on how well operators follow specifications—AR supports this with visual cues.
-
Step-by-step overlays guide workers during complex assembly or installation tasks.
-
Reduces the need for referencing printed manuals or digital screens, allowing hands-free operation.
-
Real-time error detection through AR-integrated systems enables instant corrections and quality assurance.
Minimizing Downtime with Real-Time Guidance
Operational disruptions due to mistakes or unclear procedures can be minimized with AR-based assistance.
-
Technicians can receive real-time instructions while performing maintenance or troubleshooting.
-
Remote experts can provide live support through AR devices, speeding up repairs and reducing delays.
-
Interactive diagnostics reduce guesswork, making operations more efficient.
Supporting Compliance and Standardization
Consistency across multiple teams and facilities is essential for quality and regulatory compliance.
-
AR ensures all operators follow the same visualized workflows, reducing variability.
-
Training modules embedded in AR systems promote uniform knowledge across the workforce.
-
Helps track adherence to safety and operational standards through usage data and logs.
Preparing the Workforce for Smart Factory Integration
AR is a foundational tool for upskilling workers in automated and connected environments.
-
Workers learn to interact with IoT-enabled machines and sensors via intuitive AR interfaces.
-
Blends physical and digital systems, reinforcing Industry 4.0 practices.
-
Encourages ongoing learning and faster adaptation to new equipment or protocols.
Conclusion
The application of advanced AR in manufacturing is proving to be a powerful tool for improving both safety and precision in industrial settings. By providing contextual, real-time guidance and visual aids, AR helps reduce errors, prevent accidents, and streamline complex tasks. As manufacturing continues to evolve with automation and digital technologies, augmented reality stands out as a key enabler of a safer, smarter, and more productive workplace.