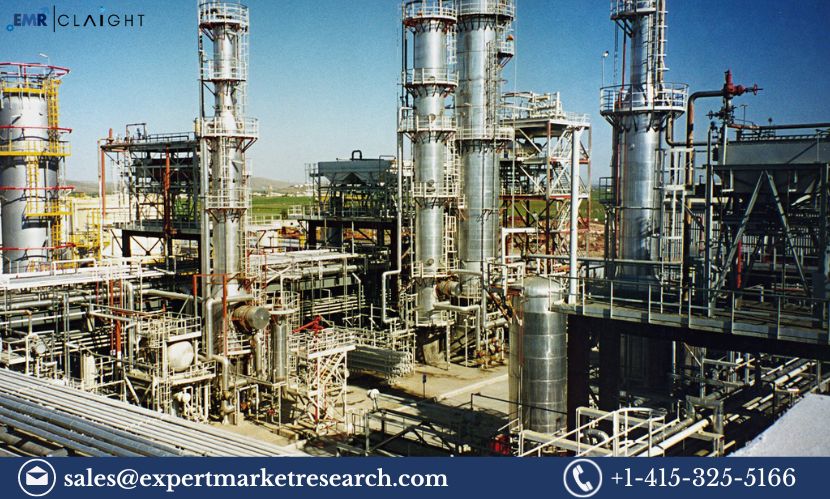
Linear Alkyl Benzene (LAB) is an organic compound widely used as a key ingredient in the production of detergents and cleaning products. It is a crucial raw material for producing linear alkylbenzene sulfonate (LAS), the most common surfactant used in household and industrial cleaning products. Setting up a Linear Alkyl Benzene (LAB) Manufacturing Plant involves understanding the production process, required raw materials, technology, and market dynamics. This article provides a detailed Linear Alkyl Benzene Manufacturing Plant Project Report, covering essential components, production processes, and important considerations for successfully establishing a LAB manufacturing facility.
What is Linear Alkyl Benzene (LAB)?
Linear Alkyl Benzene (LAB) is an organic compound formed by the alkylation of benzene with linear mono-olefins, typically derived from kerosene. LAB is the main precursor in producing linear alkylbenzene sulfonate (LAS), a biodegradable surfactant commonly found in laundry detergents, dishwashing liquids, and various cleaning agents. Due to its cost-effectiveness, stability, and biodegradability, LAB is the preferred choice for surfactant production globally.
Key Advantages of Linear Alkyl Benzene (LAB)
- Biodegradability: LAB and its derivatives are biodegradable, making them environmentally friendly compared to other non-biodegradable surfactants.
- Versatility: LAB is used to produce various cleaning agents and industrial cleaners due to its effectiveness in breaking down oils and dirt.
- Cost-Effective: LAB is economical to produce, making it a cost-effective choice for large-scale detergent production.
- Stability: LAB exhibits excellent chemical stability, allowing it to maintain its properties under various conditions, such as in hard water or high temperatures.
Get a Free Sample Report with Table of Contents @
Components of a Linear Alkyl Benzene Manufacturing Plant
Setting up a Linear Alkyl Benzene Manufacturing Plant requires various components to ensure efficient production and high-quality output. The plant must have a structured system for raw material sourcing, production equipment, and quality control systems. Below is a detailed breakdown of these elements.
1. Raw Material Procurement
The primary raw materials used in LAB production are kerosene-derived linear paraffins and benzene. The quality and purity of these raw materials are critical in determining the efficiency of the production process and the quality of the final product.
- Linear Paraffins: Derived from kerosene through processes such as hydrocracking and hydrodealkylation, linear paraffins are the key feedstock for LAB production.
- Benzene: Benzene, a petrochemical derived from crude oil or natural gas, is reacted with linear paraffins to produce LAB.
- Catalysts: Acidic catalysts, such as hydrogen fluoride (HF) or aluminum chloride, are used in the alkylation reaction to enhance the yield of LAB.
2. Production Line Setup
The production of LAB involves several critical processes, including the refining of paraffins, alkylation, and separation of by-products. Below are the major components of the production line:
- Hydrotreatment Unit: The linear paraffins are first treated in a hydrotreatment unit to remove impurities and improve the quality of the feedstock for further processing.
- Dehydrogenation Reactor: The treated paraffins are dehydrogenated to form linear olefins, which are more reactive and suitable for the alkylation process.
- Alkylation Reactor: In the alkylation reactor, linear olefins are reacted with benzene in the presence of a catalyst, such as hydrogen fluoride (HF) or aluminum chloride. This reaction forms LAB as the primary product.
- Separation and Purification Units: After the alkylation reaction, the mixture is sent through separation units to isolate LAB from by-products such as unreacted benzene and olefins. LAB is then purified to achieve the required quality for industrial use.
- Recycling Units: Unreacted benzene and olefins are recycled back into the system to improve efficiency and reduce waste.
3. Quality Control Systems
Quality control is essential in the production of LAB to ensure that the final product meets industry standards for surfactant production. Key quality control measures include:
- Raw Material Testing: The quality and purity of linear paraffins and benzene are regularly tested to ensure consistent production quality.
- Process Monitoring: Automated systems monitor the temperature, pressure, and chemical reactions during the hydrotreatment, dehydrogenation, and alkylation processes to ensure optimal conditions.
- Final Product Testing: The LAB is tested for purity, chemical composition, and performance characteristics to ensure it meets the specifications required for use in detergents and other applications.
4. Environmental Control Systems
LAB production involves the use of hazardous chemicals such as benzene and hydrogen fluoride (HF), which must be carefully managed to minimize environmental impact. Environmental control systems are essential to ensure that the plant complies with safety regulations and environmental standards.
- Emission Control Systems: Systems are in place to capture and neutralize any hazardous gases or fumes generated during production.
- Waste Management Systems: Proper handling and disposal of chemical waste, including spent catalysts and by-products, are critical to preventing environmental contamination.
- Energy Efficiency Measures: Optimizing energy consumption through heat recovery systems and energy-efficient technologies can reduce the plant’s carbon footprint and operational costs.
5. Packaging and Distribution
Once LAB is produced, it is typically stored in liquid form and transported in bulk containers, drums, or tanks, depending on customer requirements. Proper packaging ensures that the LAB is protected from contamination during storage and transportation. The packaging must also comply with safety standards due to the flammable and hazardous nature of the chemicals involved.
Linear Alkyl Benzene Manufacturing Process
The manufacturing of LAB involves several key steps, including the treatment of raw materials, the alkylation reaction, and the separation of by-products. Below is an overview of the main stages in the production process:
1. Raw Material Treatment
The process begins with the hydrotreatment of linear paraffins to remove impurities such as sulfur, nitrogen, and other contaminants. The purified paraffins are then dehydrogenated to form linear olefins, which are the reactive species required for alkylation with benzene.
2. Alkylation Reaction
In the alkylation reactor, the linear olefins are reacted with benzene in the presence of an acid catalyst, such as hydrogen fluoride (HF) or aluminum chloride. The reaction results in the formation of LAB, along with some by-products, including unreacted benzene and olefins.
3. Separation and Purification
After the alkylation reaction, the mixture is sent through separation units to recover LAB from the by-products. The unreacted benzene and olefins are separated and recycled back into the system. The LAB is then purified to remove any remaining impurities, ensuring that it meets the necessary quality standards.
4. Storage and Packaging
The purified LAB is stored in tanks or drums for transportation and distribution. Proper storage conditions are critical to prevent contamination and ensure the safety of the product during handling.
Key Considerations for Setting Up a Linear Alkyl Benzene Manufacturing Plant
Establishing a Linear Alkyl Benzene Manufacturing Plant involves careful planning and consideration of various factors that can influence the plant’s success. Below are some key factors to consider when setting up such a facility:
1. Location
The location of the plant is critical for ensuring access to raw materials, energy, and transportation infrastructure. Proximity to petrochemical refineries can reduce the cost of raw materials such as kerosene and benzene. Additionally, the plant should be located near major transportation routes for the efficient distribution of the final product.
2. Technology and Equipment
Investing in modern, efficient production technologies is essential for ensuring high-quality LAB and minimizing production costs. Advanced equipment can improve the efficiency of the dehydrogenation and alkylation processes, reduce waste, and enhance energy recovery. Automation and process control systems are also crucial for maintaining consistent product quality and ensuring safety.
3. Market Research
Before setting up a LAB manufacturing plant, it is important to conduct thorough market research to understand the demand for LAB in various industries, including household detergents, industrial cleaners, and other surfactants. Understanding regional demand, competition, and customer preferences will help manufacturers tailor their production capacities and product offerings to meet market needs.
4. Environmental Impact
The production of LAB involves hazardous chemicals that can have significant environmental impacts if not managed properly. Manufacturers must implement environmentally friendly practices, such as emission control, waste treatment, and recycling systems, to minimize the plant’s environmental footprint. Compliance with local and international environmental regulations is essential for the long-term sustainability of the plant.
5. Regulatory Compliance
Given the hazardous nature of chemicals like benzene and hydrogen fluoride, regulatory compliance is crucial in LAB manufacturing. Manufacturers must ensure that the plant complies with safety regulations for chemical handling, worker protection, and environmental management. Proper labeling and documentation are also essential for ensuring that the final product meets industry standards for surfactant production.
FAQ
1. What is a Linear Alkyl Benzene Manufacturing Plant Project Report?
A Linear Alkyl Benzene Manufacturing Plant Project Report is a detailed document outlining the process of setting up a LAB production facility. It covers aspects such as raw material procurement, production processes, equipment, market analysis, and regulatory compliance.
2. What are the main applications of Linear Alkyl Benzene?
Linear Alkyl Benzene (LAB) is primarily used in the production of linear alkylbenzene sulfonate (LAS), a key surfactant in household detergents, industrial cleaners, and other personal care products.
3. What factors should be considered when setting up a Linear Alkyl Benzene manufacturing plant?
Key factors include the plant’s location, access to raw materials, technology used in production, environmental impact, and market demand for LAB.
4. How is quality controlled in Linear Alkyl Benzene production?
Quality control involves testing raw materials, monitoring chemical reactions during the hydrotreatment, dehydrogenation, and alkylation processes, and ensuring the final product meets industry standards for purity and performance.
5. What are the environmental considerations in Linear Alkyl Benzene manufacturing?
Environmental considerations include managing hazardous emissions, reducing waste through recycling, and implementing energy-efficient technologies to minimize the plant’s carbon footprint.
Related Reports
https://www.expertmarketresearch.com/reports/5g-iot-market
https://www.expertmarketresearch.com/articles/top-5-companies-in-the-global-neotame-market
https://www.expertmarketresearch.com/reports/gas-treatment-market
Media Contact:
Company Name: Claight Corporation
Contact Person: Lewis Fernandas, Corporate Sales Specialist — U.S.A.
Email: [email protected]
Toll Free Number: +1–415–325–5166 | +44–702–402–5790
Address: 30 North Gould Street, Sheridan, WY 82801, USA
Website: www.expertmarketresearch.com
Aus Site: https://www.expertmarketresearch.com.au