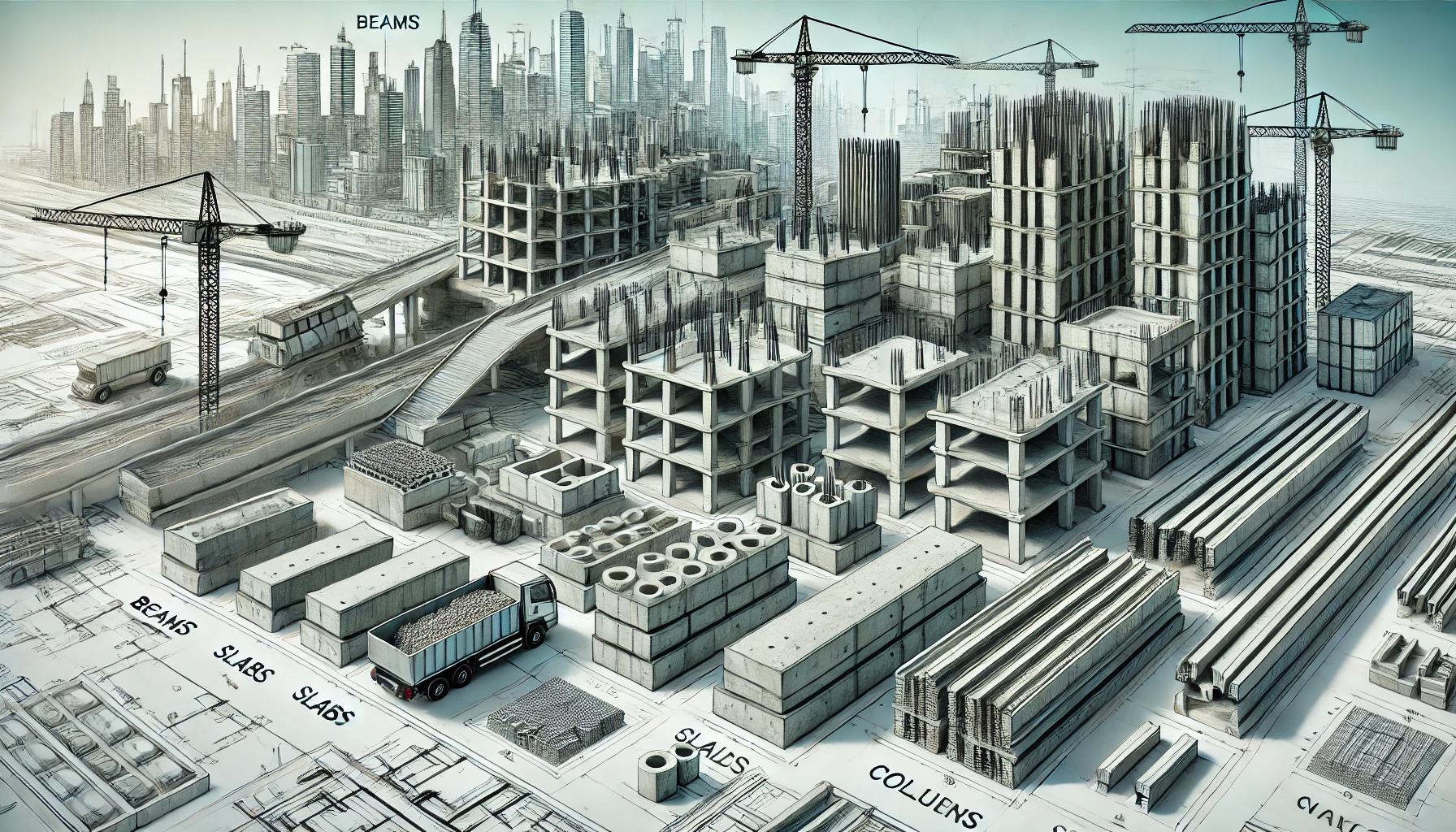
Precast concrete components are transforming the construction industry, making building projects faster, stronger, and more cost-effective than ever before. From high-rise apartments to massive bridges, precast technology is setting new standards in efficiency and durability.
But what exactly are precast concrete components? Why are they gaining traction globally? And how can they enhance your construction projects?
This comprehensive guide will answer all these questions and more. Whether you’re a builder, architect, or investor, you’ll discover why precast is the future of construction.
🔥 Key Takeaways
- Precast concrete components are factory-made building elements transported to construction sites.
- They are faster to install, stronger, and more cost-effective than traditional cast-in-place concrete.
- Common types include beams, slabs, walls, columns, stairs, and facades.
- Used extensively in residential, commercial, and infrastructure projects.
- Innovations in precast technology are making construction greener and more efficient.
📌 What Are Precast Concrete Components?
Precast concrete components are prefabricated building elements made in a controlled factory environment and then transported to construction sites for installation. Unlike cast-in-place concrete, which is poured and cured on-site, precast elements are pre-engineered and ready for assembly.
Imagine building with giant Lego blocks—that’s how precast components work! They are custom-designed to fit specific project needs, ensuring precision, quality, and durability.
🔗 Related Read: Introduction to Precast Detailing
🔄 Precast vs. Cast-in-Place Concrete: What’s the Difference?
Feature | Precast Concrete | Cast-in-Place Concrete |
---|---|---|
Manufacturing | Made in a factory | Poured and cured on-site |
Construction Time | Faster assembly | Longer curing time |
Quality Control | High precision | More room for variation |
Weather Dependence | Minimal impact | Affected by weather |
Labor Requirement | Lower labor cost | Higher labor cost |
🔗 More Insights: How Precast Detailing Can Eliminate Costly On-Site Errors
🚀 Why Choose Precast Concrete Components?
✅ 1. Faster Construction
Precast elements are manufactured in advance, reducing on-site construction time by up to 50%. This is a game-changer for projects with tight deadlines.
✅ 2. Superior Strength & Durability
Precast components are cured in controlled environments, leading to higher strength and longevity compared to traditional concrete. Many structures built with precast concrete last 50 to 100 years.
✅ 3. Cost-Effective Solution
Although the initial cost is higher, precast concrete reduces labor costs, material waste, and construction errors, saving money in the long run.
✅ 4. Better Quality Control
Manufacturing in controlled factory conditions ensures precision, uniformity, and minimal defects, unlike on-site pouring, which is prone to inconsistencies.
✅ 5. Eco-Friendly & Sustainable
- Less material waste due to factory precision.
- Energy-efficient production using sustainable materials.
- Recyclable at the end of its lifecycle.
🔗 Industry Insights: 2025 Trends in Precast Concrete Detailing
🏗️ Types of Precast Concrete Components
1️⃣ Precast Beams
Precast beams provide structural support in buildings and bridges.
- Types: I-beams, T-beams, L-beams
- Uses: Bridges, commercial buildings, parking garages
2️⃣ Precast Slabs
Used for floors and roofs, precast slabs enhance load-bearing efficiency.
- Types: Hollow-core, solid, double-T slabs
- Uses: High-rise buildings, parking decks, stadiums
3️⃣ Precast Walls
Precast walls offer both structural and decorative functions.
- Types: Load-bearing, non-load-bearing, insulated panels
- Uses: Factories, malls, apartment buildings
4️⃣ Precast Columns
Precast columns bear the vertical load in structures.
- Uses: Multi-story buildings, bridges, industrial facilities
5️⃣ Other Precast Components
- Precast Stairs: Quick installation for high-rise buildings.
- Precast Facades: Enhances aesthetics and energy efficiency.
- Precast Foundations: Ensures stability and durability.
🔬 How Are Precast Concrete Components Made?
1️⃣ Mold Creation – A mold is designed based on specifications.
2️⃣ Concrete Pouring – High-strength concrete is poured into the mold.
3️⃣ Reinforcement – Steel reinforcements are added for strength.
4️⃣ Curing Process – Concrete is cured under optimal temperature and humidity.
5️⃣ Quality Control – Components undergo rigorous testing.
6️⃣ Transportation & Installation – Once approved, they are delivered to the site for assembly.
🔗 Expert Services: Need Precast Detailing? Let’s Talk!
❓ Frequently Asked Questions (FAQs)
🏗️ Is Precast Concrete Stronger Than Traditional Concrete?
Yes! Factory-controlled curing makes precast components denser and stronger than cast-in-place concrete.
⏳ How Long Does Precast Concrete Last?
With proper maintenance, precast concrete can last 50 to 100 years.
💰 Is Precast Concrete Expensive?
While initial costs may be higher, faster construction, reduced labor, and lower material waste make it cost-effective over time.
🛠️ Can Precast Concrete Be Customized?
Absolutely! Precast components can be designed in various shapes, textures, and finishes to match architectural styles.
📚 External Resources for Further Reading
- National Precast Concrete Association (NPCA): https://precast.org
- Sustainable Precast Concrete: https://www.sustainableprecast.ca
📞 Need Expert Precast Detailing Services? Let’s Talk!
✅ Accurate precast detailing to eliminate costly errors
✅ Faster construction timelines with pre-engineered solutions
✅ Quality-assured components designed for maximum durability
Conclusion
Precast concrete components are reshaping the future of construction. Their strength, speed, and sustainability make them the ideal choice for modern building projects. As technology continues to evolve, precast will only become more advanced and widely used.
If you’re considering precast concrete for your next project, ensure you work with experienced precast detailing professionals to maximize its benefits.
Learn about Skip Hire for Construction Projects: Streamlining Waste Management on Site