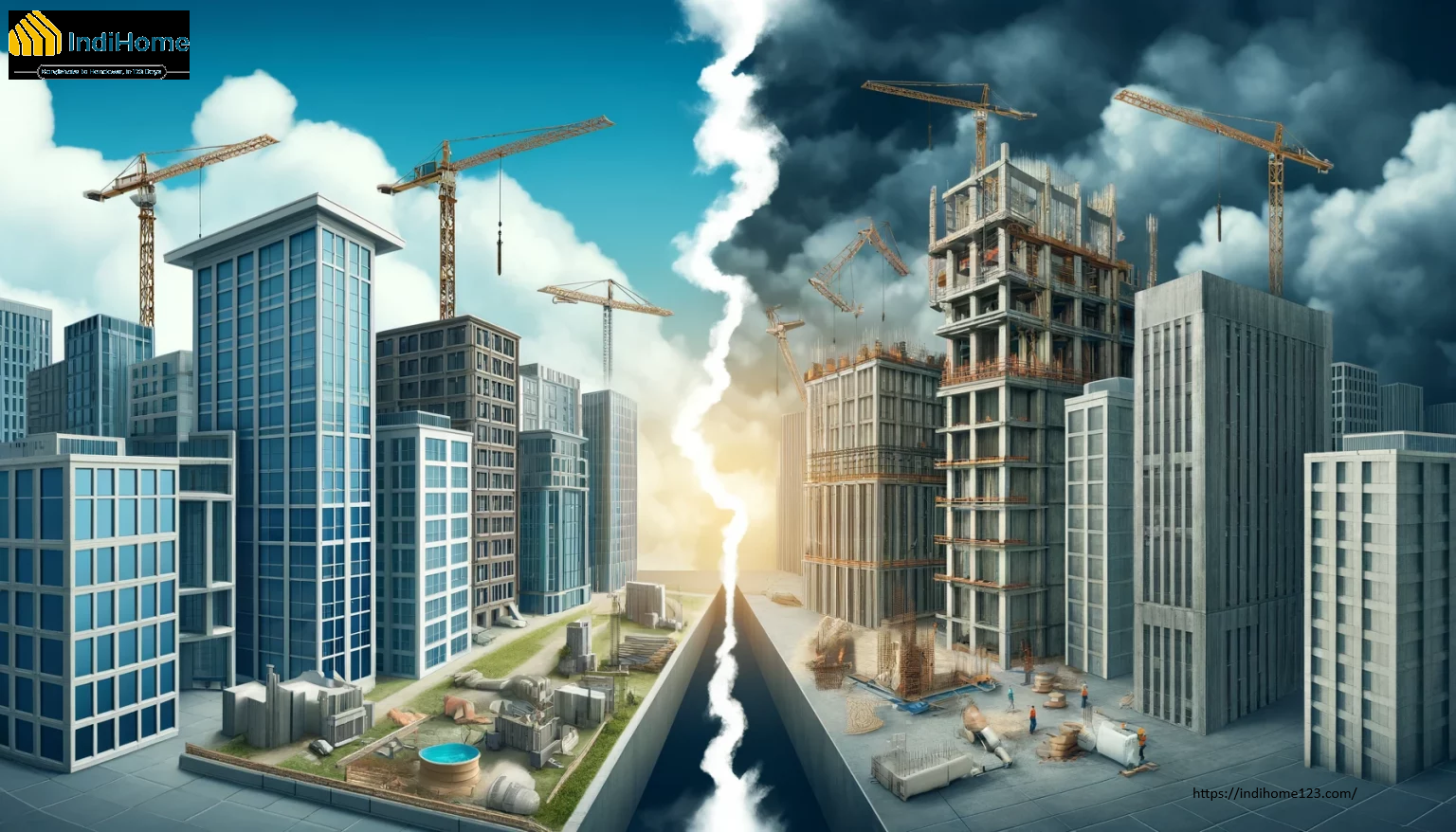
Construction methods have evolved significantly over the years, offering builders more efficient and cost-effective solutions. Two of the most common methods used today are precast building construction and conventional construction. While both approaches serve the same purpose—creating durable structures—they differ significantly in terms of materials, speed, cost, and overall efficiency.
What is Precast Building Construction? Precast building construction involves manufacturing structural elements such as walls, beams, and slabs in a controlled factory environment before transporting them to the construction site for assembly. This method enhances efficiency, minimizes on-site labor, and ensures higher quality due to stringent quality control measures in the factory.
Advantages of Precast Construction:
-
Faster Construction – Since components are manufactured off-site, on-site assembly is much quicker, reducing overall project duration.
-
High Quality & Durability – Factory-controlled environments ensure precision and quality, leading to stronger and more durable structures.
-
Less Waste – Precast construction reduces material wastage compared to traditional methods.
-
Weather-Resistant – Manufacturing in a controlled environment eliminates delays due to weather conditions.
-
Cost Efficiency – Although the initial investment might be high, savings on labor and time make it a cost-effective choice. What is Conventional Construction? Conventional construction, also known as cast-in-place or in-situ construction, involves building the structure on-site from scratch. This method uses a framework of formwork, reinforcing bars, and poured concrete to create the desired structure. Advantages of Conventional Construction:
-
Flexibility in Design – Allows for modifications and customizations as construction progresses.
-
Lower Initial Costs – Does not require investment in molds or precast facilities.
-
Easier for Small-Scale Projects – Suitable for areas with limited access to precast manufacturing plants.
-
Widely Accepted – Traditional techniques are well understood by laborers and contractors.
Key Differences Between Precast and Conventional Construction
Feature
|
Precast Construction
|
Conventional Construction
|
Construction Speed
|
Faster due to pre-manufactured components
|
Slower as construction happens on-site
|
Cost
|
Lower in the long run, but higher initial investment
|
Higher overall due to labor and time costs
|
Quality Control
|
Higher due to factory conditions
|
Varies based on site conditions
|
Labor Requirement
|
Requires fewer workers on-site
|
Requires more on-site labor
|
Environmental Impact
|
Less waste, more eco-friendly
|
More material wastage
|
Weather Dependence
|
Minimal impact from weather
|
Can be delayed due to bad weather
|
Precast House Price vs. Conventional House Price
One of the most common concerns when choosing between these two methods is the cost factor. The precast house price varies based on factors such as materials, location, and labor. Typically, precast homes are 5-20% cheaper than conventional homes in the long run due to reduced labor and faster construction. However, the initial costs may be higher because of the need for molds and transportation.
In contrast, conventional houses may have lower initial costs but tend to incur higher expenses in labor, extended construction timelines, and potential delays due to weather or material procurement issues.
Which One Should You Choose?
The choice between precast and conventional construction depends on several factors, including budget, timeline, and project scale.
• If you need a fast, durable, and cost-effective solution, precast construction is ideal.
• If you prioritize flexibility and on-site modifications, conventional construction might be a better option.
In conclusion,
precast building construction is a modern, efficient, and increasingly popular method that offers significant benefits over conventional construction. While precast house prices may seem higher initially, they provide cost savings in the long run, making them a smart investment for many builders and homeowners.